Introduction
Effective manufacturing asset management is critical for minimizing downtime and maximizing the lifespan of your equipment. Predictive maintenance typically reduces machine downtime by 30 to 50% and extends machine life by 20 to 40%, demonstrating the tangible benefits of a data-driven approach to asset management.
Amid relentless market pressures and escalating operating costs, every minute of downtime and every unplanned maintenance expense can significantly erode profitability.
This guide defines manufacturing asset management, outlines its essential components and best practices, and offers actionable strategies to enhance asset performance and drive operational excellence.
What Is Manufacturing Asset Management?
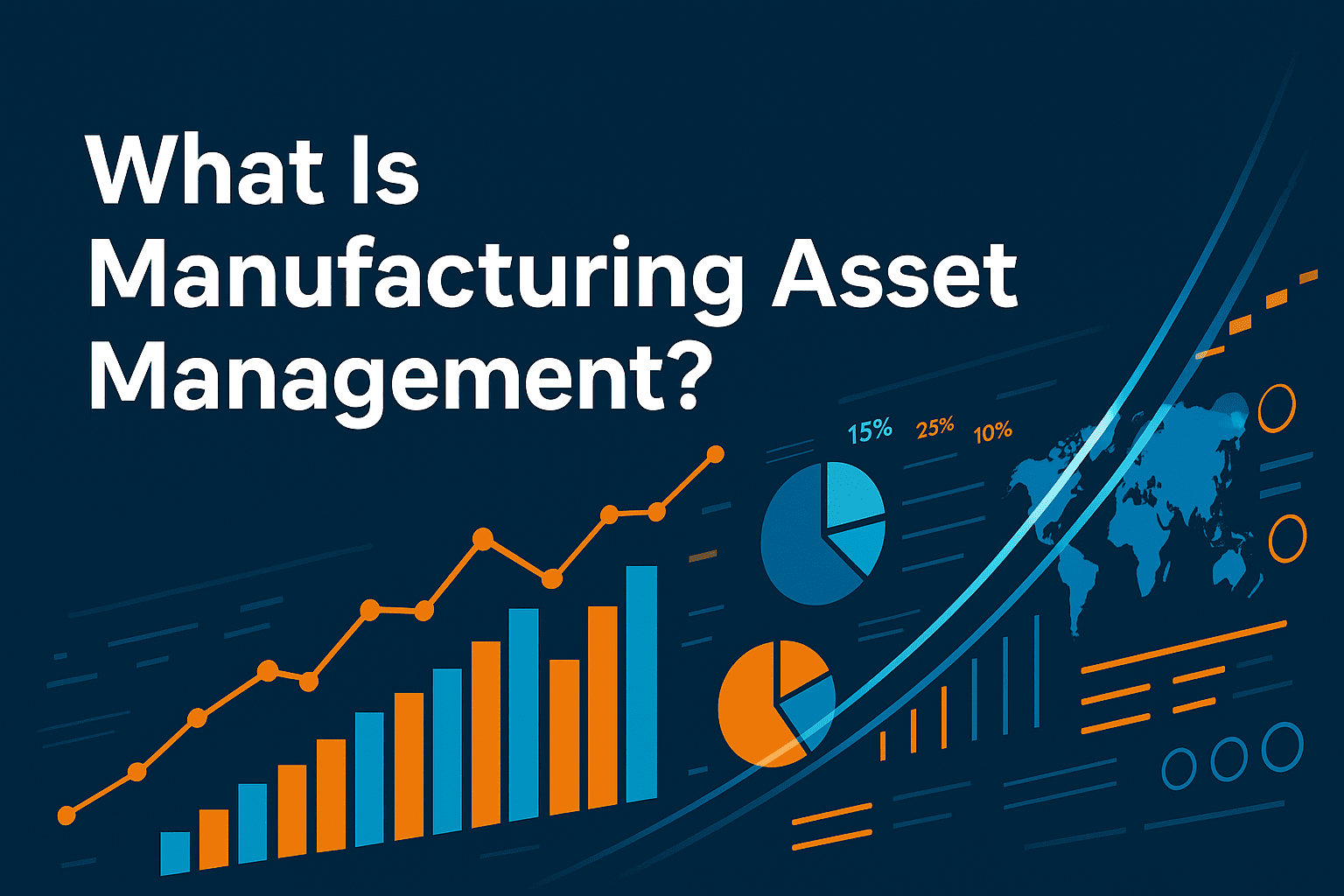
Manufacturing Asset Management (MAM) is the systematic process of acquiring, operating, maintaining, and disposing of physical assets throughout their lifecycle in a manufacturing environment. This includes equipment, machinery, tools, and infrastructure that are essential for production processes.
Key Components of Asset Management In Manufacturing
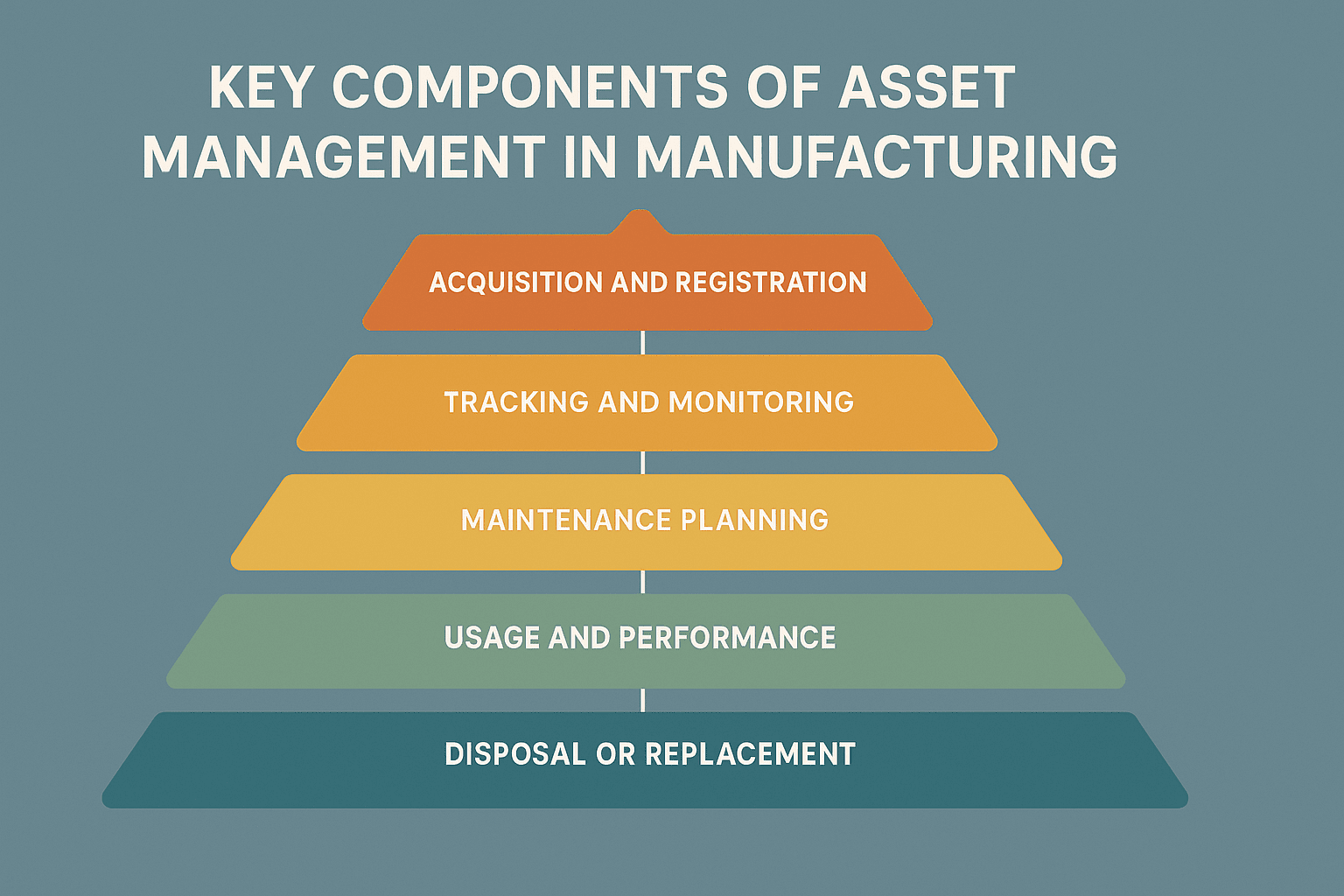
Effective asset management is essential for enterprise manufacturers to maximize operational efficiency and minimize costs throughout the lifecycle of industrial assets. Below are the core components of a robust manufacturing asset management strategy:
1. Acquisition and Registration
Implement rigorous protocols for procuring and registering all industrial assets. Every piece of equipment should be logged into a centralized system with detailed specifications. This ensures full traceability from acquisition, providing a strong foundation for strategic asset management and lifecycle decisions.
2. Tracking and Monitoring
Utilize real-time tracking solutions to monitor asset location, status, and performance continuously. Advanced monitoring systems enable timely interventions by flagging potential issues before they escalate. This persistent oversight ensures that all assets remain aligned with production needs and operational requirements.
3. Maintenance Planning
Develop a proactive maintenance schedule driven by data and predictive analytics. Regular, planned maintenance minimizes unexpected downtime and extends equipment lifespan. A disciplined approach to maintenance planning secures operational continuity and safeguards your capital investment.
4. Usage and Performance
Measure asset utilization and performance consistently to ensure optimal efficiency. Detailed performance metrics help identify underutilized and idle equipment and highlight areas for improvement. This ongoing evaluation supports informed decisions that optimize production output and reduce operational inefficiencies.
5. Compliance and Records
Maintain comprehensive documentation on each asset’s performance, maintenance history, and regulatory compliance. Accurate records are crucial for audits and provide transparency in financial and operational reporting. This commitment to documentation mitigates risks and supports robust, data-driven decision-making.
6. Disposal or Replacement
Establish clear criteria for disposing of or replacing excess and obsolete (E&O) or underperforming assets. A systematic approach to asset liquidation ensures that surplus inventory is efficiently removed, freeing up capital and storage space. By timing asset replacements strategically, you maintain a lean and resilient production environment.
Why Asset Management in Manufacturing Matters
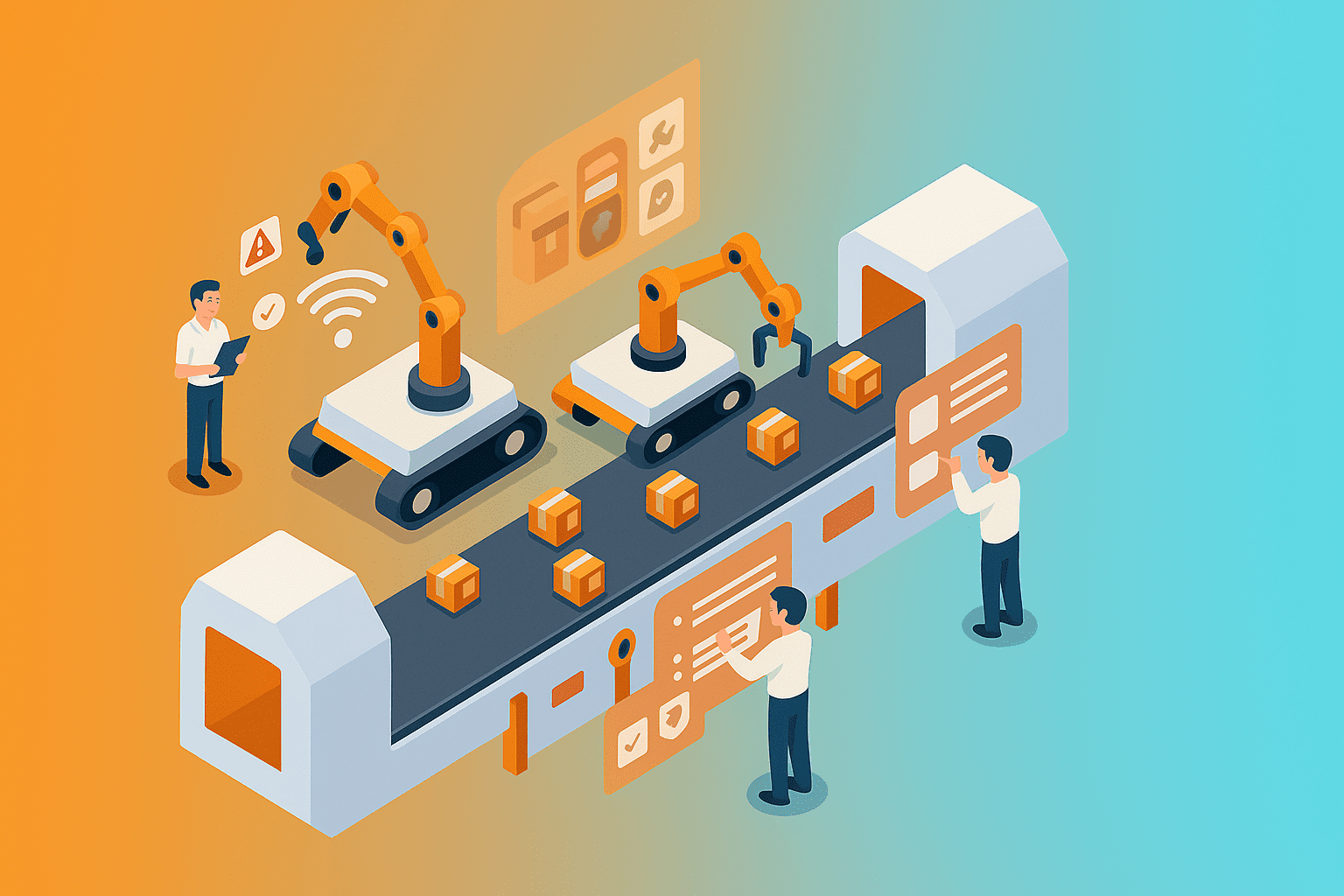
Effective manufacturing asset management is crucial for maintaining uninterrupted production and controlling costs. Below are the specific benefits that make asset management a critical operational priority.
1. Reduces Unplanned Downtime
Unexpected equipment failures can bring production to a standstill, resulting in significant revenue loss. A structured asset management process schedules regular maintenance and enables early detection of potential issues, substantially reducing downtime. This proactive approach is critical for keeping production lines operational and maintaining customer satisfaction.
2. Improves Resource Planning
Without real-time visibility into asset conditions, planning remains reactive and leads to inefficiencies such as duplicate purchases or excessive inventory across sites. A comprehensive asset management strategy optimizes resource planning by aligning stock levels with actual operational needs. This ensures that every asset contributes effectively to overall production and cost management.
3. Cuts Maintenance Costs
Reactive maintenance strategies often lead to unexpected expenses and emergency repairs that drain your budget. By implementing preventive maintenance based on condition-based data, you can reduce costly downtime and extend the lifespan of your equipment. This approach not only lowers maintenance costs but also improves the return on your capital investments.
4. Supports Capital Allocation
Accurate tracking of asset performance provides the insights needed to determine when equipment should be replaced, upgraded, or repurposed. This data-driven perspective prevents over-investment in redundant assets and optimizes capital allocation toward strategic growth initiatives. Proper capital allocation ensures that funds are directed to projects that enhance operational resilience and profitability.
5. Strengthens Operational Control
A standardized manufacturing asset management framework delivers consistency across multiple sites by providing a unified view of asset performance. This consistency minimizes reporting discrepancies, streamlines maintenance execution, and enhances overall operational control. Improved control facilitates scalable growth while ensuring that every aspect of your asset base is managed efficiently.
Common Challenges in Asset Management in the Manufacturing Industry
.png)
Even with clear benefits, manufacturers face several obstacles when harnessing effective asset management.
1. Manual Tracking
Relying on spreadsheets or paper-based logs may lead to inefficiencies and errors in asset management. Without a centralized digital system, teams lack consistent, real-time information. This often leads to missed updates, delays, and operational disruptions.
2. Data Silos
When departments manage assets independently, records become fragmented and inconsistent. The absence of cross-functional integration prevents a unified view of asset status, usage, and location. This disconnect slows decision-making and increases the risk of redundant or conflicting actions, undermining overall asset control.
3. Low Adoption of Technology
Resistance to new digital systems often stems from unfamiliarity and perceived complexity. Without clear, role-specific training and seamless integration into existing workflows, technology remains underutilized. This limits the potential impact of modern asset management solutions and hampers long-term improvements.
4. Cost Barriers
High upfront investments in asset management systems can deter immediate adoption, particularly for budget-conscious operations. However, delaying technological upgrades often leads to higher long-term costs due to unplanned repairs, downtime, and lost productivity. Whereas cumulative inefficiencies outweigh short-term savings.
5. Unstructured Asset Disposal
A lack of clear protocols for retiring obsolete assets poses significant challenges for enterprise manufacturers. Without standardized asset disposition processes, excess equipment often remains stored unnecessarily, leading to increased costs and potential regulatory issues. Amplio’s asset recovery solutions efficiently liquidate surplus assets by connecting you with qualified buyers, ensuring that your unused assets convert into tangible value.
Best Practices for Asset Management in Manufacturing
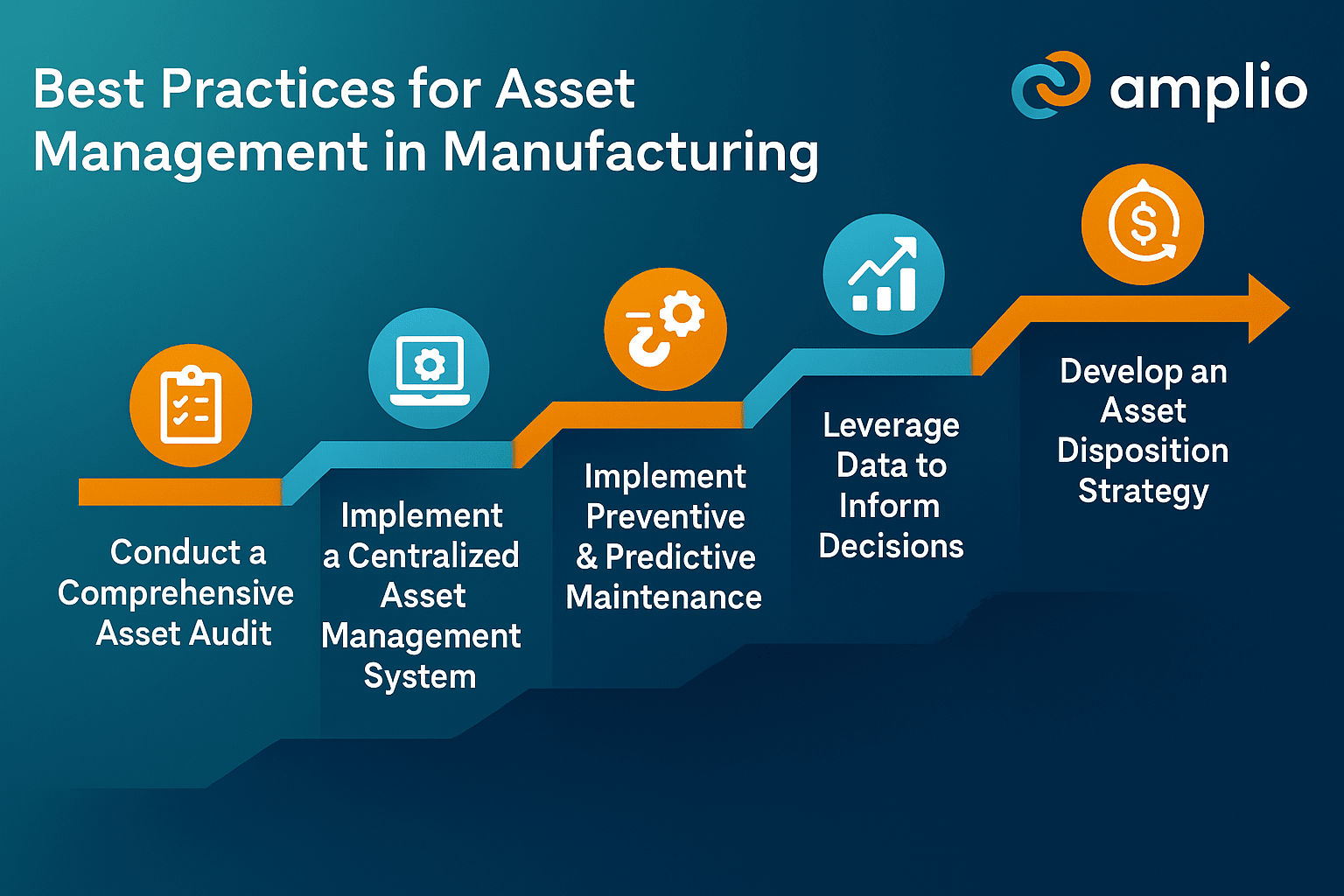
An effective asset management strategy reduces operational risk, increases visibility, and supports long-term performance objectives. The practices below provide a foundation for successful implementation:
1. Conduct a comprehensive asset audit
Performing regular, thorough asset audits is crucial. Detailed audits help you accurately identify underperforming or obsolete assets. This clarity enables informed decisions about maintenance, replacement, or disposal.
2. Implement a Centralized Asset Management System
Centralize all asset data into one unified platform to improve visibility. A centralized system streamlines tracking across sites, integrates maintenance schedules, and supports robust reporting. This enhances control and reduces errors in your asset management process.
3. Implement Preventive & Predictive Maintenance
Adopt maintenance strategies based on data and analytics. Preventive and predictive maintenance reduce unplanned downtime and extend equipment lifespan. This approach minimizes repair costs and safeguards your production continuity.
4. Leverage data to inform decisions
Utilizing real-time data and asset performance metrics is essential for strategic decision-making. A study by Emerald demonstrates that top managers actively employ business analytics to monitor performance against targets and promptly take corrective actions, while also integrating insights from stakeholder and expert feedback for future planning.
This balanced, data-driven approach equips you with optimal asset utilization and adjusts strategies efficiently, ensuring that your operations remain agile and aligned with long-term strategic goals.
5. Develop an asset disposition strategy
A well-defined asset disposition strategy is essential for managing the responsible retirement, resale, liquidation, or removal of end-of-life assets. Engaging a trusted partner like Amplio ensures compliance with regulatory requirements while maximizing value recovery. Through expert handling of asset liquidation and disposal, organizations can turn retired equipment into a strategic advantage rather than a sunk cost.
Final Thoughts
Effective manufacturing asset management strikes a balance between operational efficiency, cost control, and long-term strategy. By auditing your equipment, tracking performance, scheduling preventive maintenance, and planning for end‑of‑life disposition, you safeguard cash flow, prolong machine life, and support continuous production.
Make proactive manufacturing asset management your competitive advantage. Partner with Amplio to conduct regular procurement audits, centralize your asset data, and implement strategic maintenance and disposal processes.
To see how Amplio’s data‑driven platform can connect you with surplus assets, optimize asset performance, and reinforce your supply chain resilience, contact us now.