Green initiatives for businesses are deliberate strategies that reduce environmental impact while driving long-term operational efficiency. These initiatives include reducing waste, lowering energy consumption, and integrating sustainable materials and systems into core operations.
Businesses that embed sustainability into how they manage assets, facilities, and supply chains are seeing measurable returns across both cost and performance metrics.
In this article, we explore 10 practical green initiatives designed for industrial organizations aiming to support a greener, more sustainable economy.
1. Conduct an Asset Lifecycle Audit
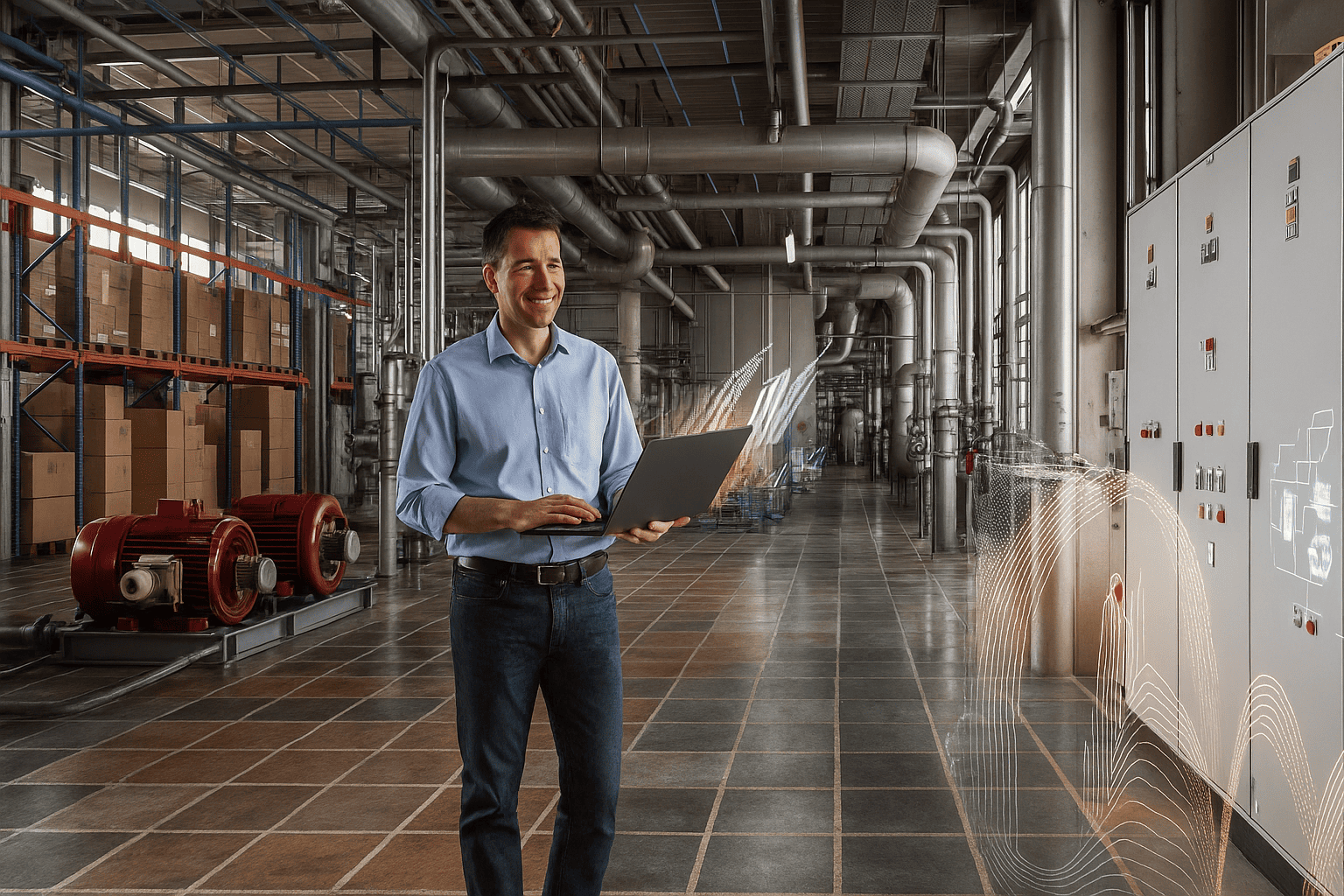
An asset lifecycle audit is a foundational step for any organization seeking to align sustainability goals with operational efficiency. It provides clarity on which assets are actively contributing to performance—and which are idle, underutilized, or ready for strategic disposition.
This visibility enables better decision-making. Businesses can prevent unnecessary equipment purchases, redeploy assets internally, and reduce waste tied to overcapacity. For capital-intensive industries, this directly supports emissions reduction, space optimization, and cost control.
Alfa Laval, a global manufacturer with over 21,000 employees, executed a structured asset audit across its global IT infrastructure. By implementing a centralized recovery and reporting system, the company extended the life cycle of critical assets, reduced waste, and recovered financial value.
2. Resell or Liquidate Surplus Industrial Equipment
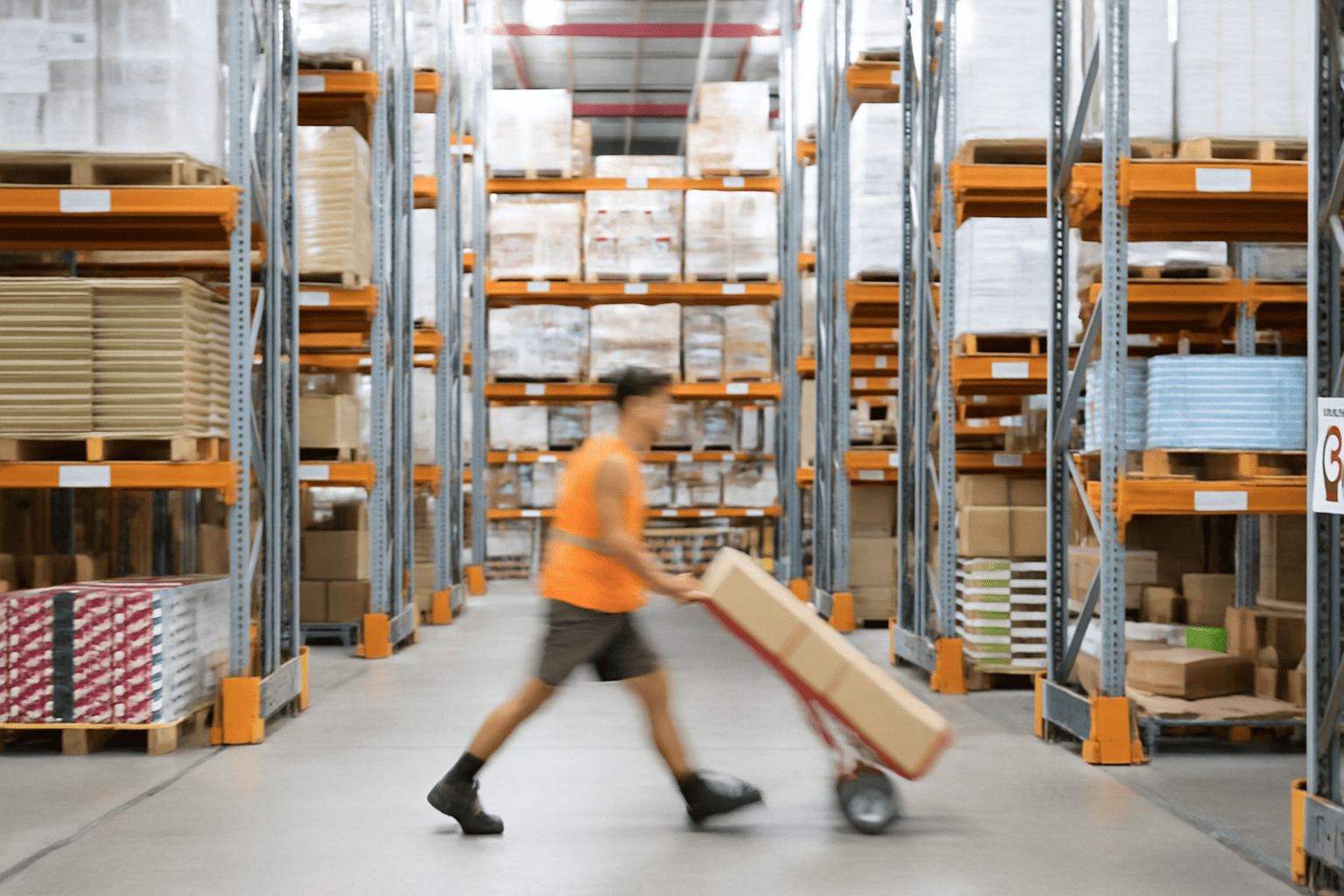
Surplus industrial equipment consumes valuable space, ties up working capital, and introduces long-term inefficiencies. When assets are no longer aligned with operational needs, holding them becomes both a financial and environmental liability. Structured liquidation or resale turns this liability into a recovery opportunity.
This strategy supports key objectives: reduced material waste, improved facility utilization, and accelerated capital reinvestment. As a green initiative idea for businesses, it strengthens circular supply chain efforts by returning equipment to productive use—avoiding premature disposal and reducing emissions tied to new manufacturing.
A plumbing manufacturer with 17 U.S. facilities partnered with Amplio to address approximately $4 million in slow-moving and obsolete inventory. Through structured resale across multiple channels, Amplio enabled full site clearance, eliminated $880,000 in annual carrying costs, and returned $70,000 in resale value. The project reduced financial drag, improved space utilization, and aligned with the company’s broader sustainability targets.
3. Adopt Smart Energy Management Solutions
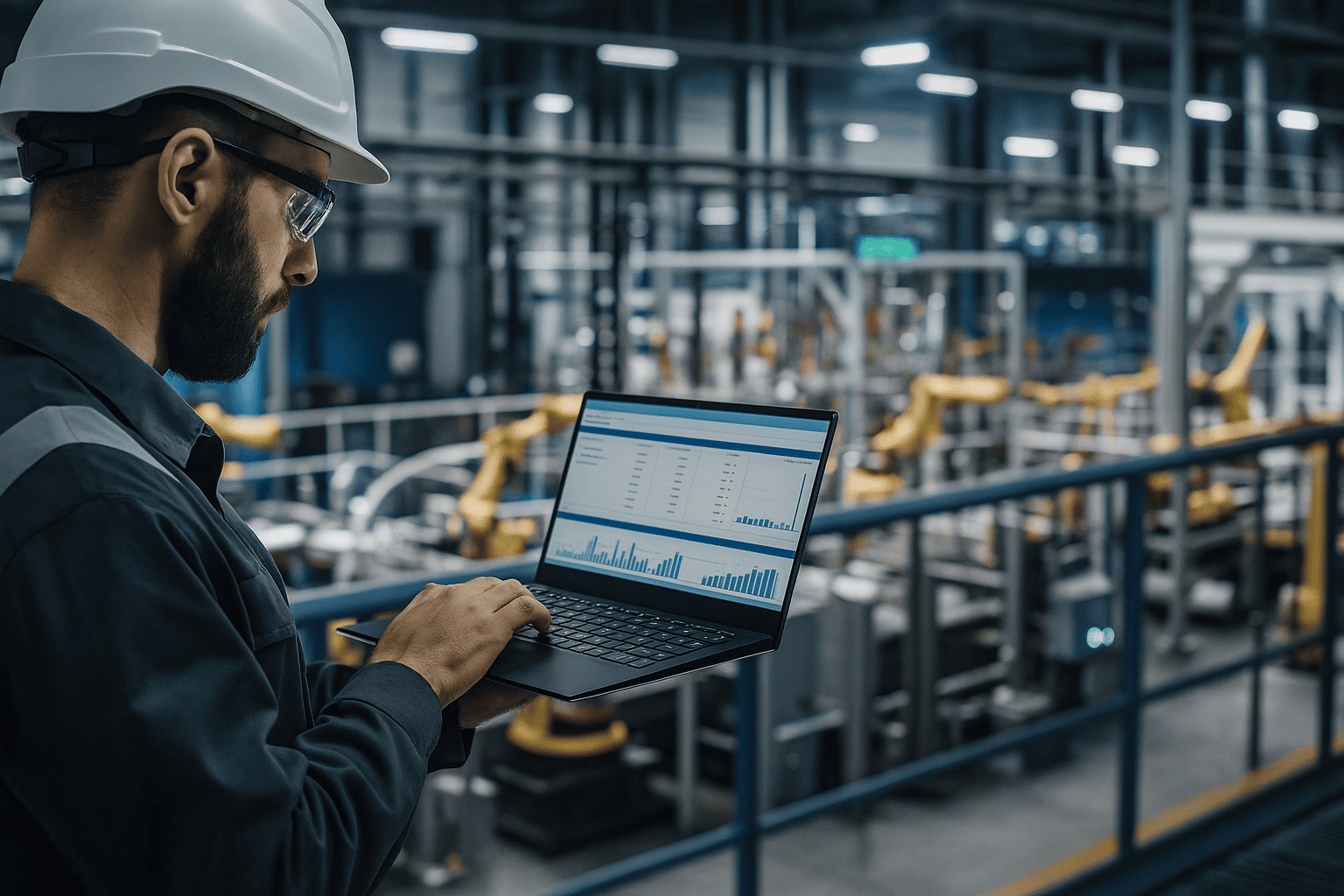
Energy remains one of the most variable and costly inputs for industrial operations. Without real-time monitoring and control, facilities often operate with excess load, unplanned consumption spikes, and limited visibility into performance. This directly impacts operating costs, asset efficiency, and sustainability metrics.
Advanced energy management systems address these challenges by aligning consumption with demand. Technologies such as smart meters, load optimization controls, and automated shutdown protocols allow manufacturers to monitor usage at the equipment level and respond in real time. These systems reduce waste, prevent overuse, and support compliance with evolving ESG requirements.
Haier Group, a global manufacturer operating across 58 production facilities, implemented a smart energy management platform based on ISO 50001. The initiative connected over 30,000 equipment units to a central analytics engine, enabling predictive load balancing and continuous performance improvement. As a result, the company reduced energy consumption per unit of output by more than 43%, cut carbon emissions by over 157,000 tons, and achieved $50 million in cost savings.
4. Transition to Low-Emission or Electric Machinery
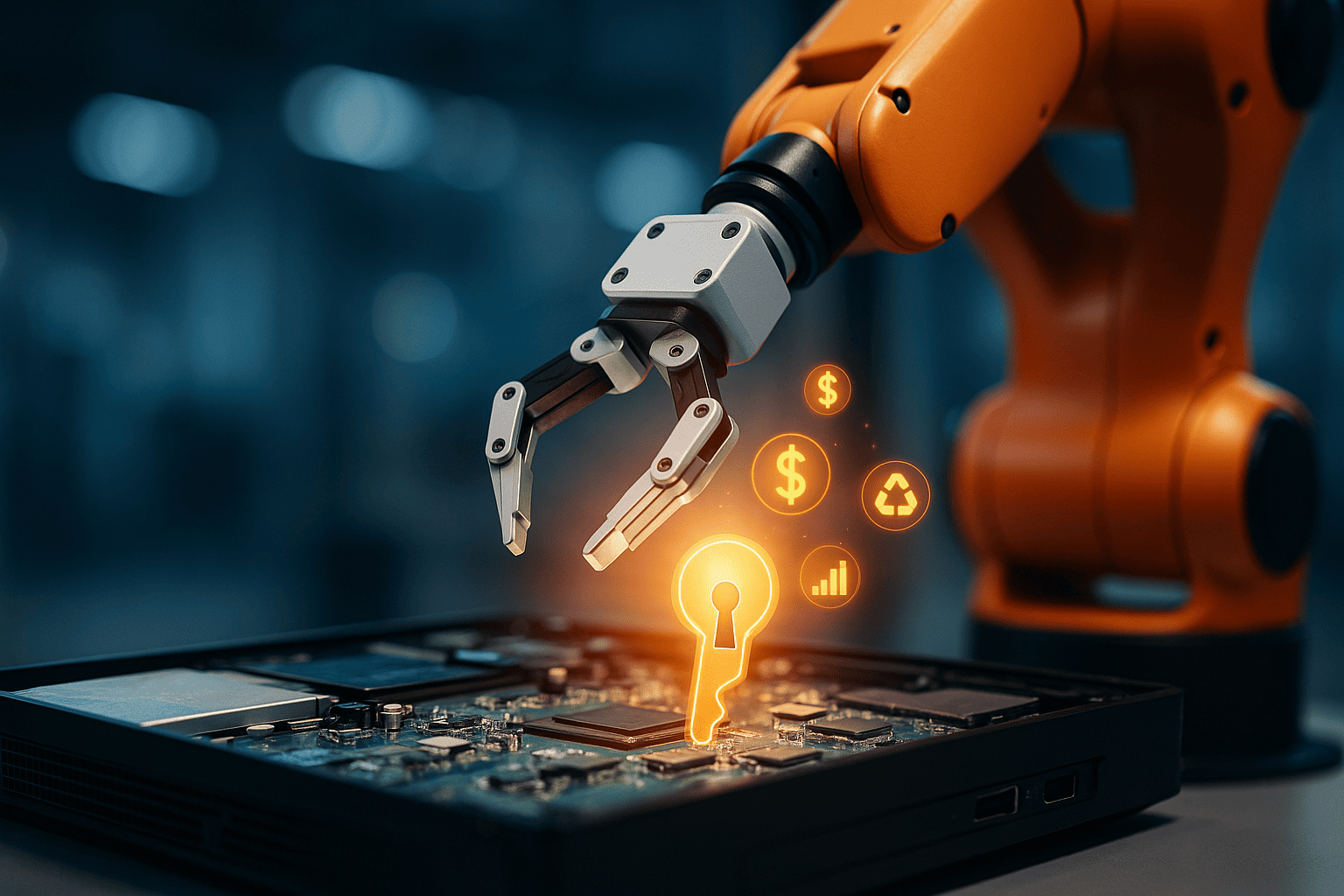
Outdated machinery is a persistent liability for industrial operators. Higher fuel consumption, increased emissions, and regulatory exposure make legacy equipment difficult to justify—both operationally and financially.
Upgrading to low-emission or electric systems is a direct path to reducing environmental impact while improving lifecycle performance. These technologies are engineered for higher energy efficiency, automation compatibility, and reduced carbon output. For manufacturers, they represent a capital investment with measurable returns—both in performance and in alignment with compliance expectations.
Boliden, a multinational mining and metals company, implemented electric trolley infrastructure in its Aitik and Kevitsa mines to reduce reliance on diesel. At Aitik, converted mine trucks and electrified haul routes cut transport-related emissions by 15% over the mine’s lifespan. Kevitsa’s implementation is projected to eliminate over 5,000 cubic meters of diesel annually. These results demonstrate how targeted equipment modernization can reduce emissions at scale while supporting operational continuity.
5. Streamline Industrial Logistics and Fleet Emissions
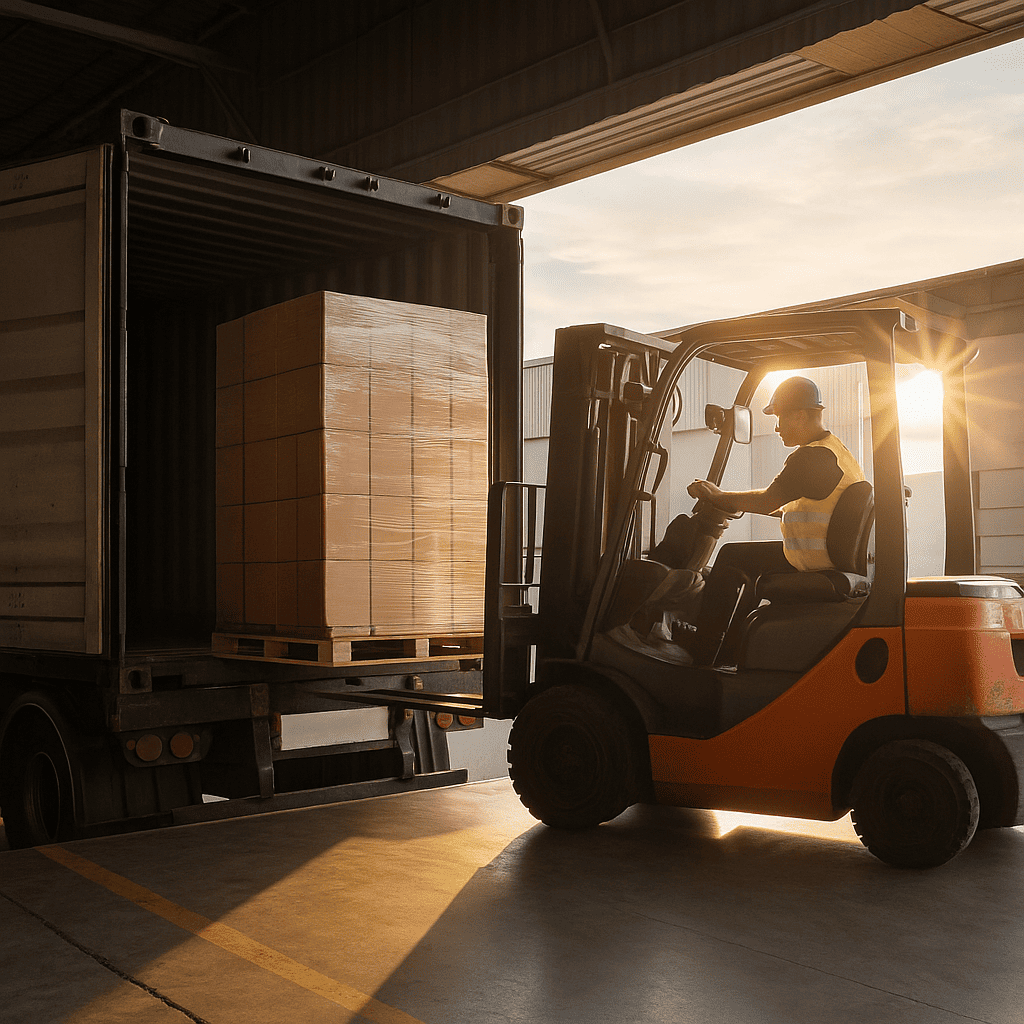
Logistics operations are a significant contributor to emissions across industrial supply chains. Without system-level optimization, manufacturers face elevated fuel consumption, underutilized routes, and growing compliance pressure tied to Scope 1 emissions.
Targeted logistics improvements—such as dynamic route planning, electrification of fleet segments, and dispatch automation—reduce transportation-related carbon impact and increase delivery efficiency. These solutions also stabilize the cost per shipment and support ESG tracking requirements across jurisdictions.
United Parcel Service (UPS), operating one of the largest industrial fleets globally, implemented a data-driven routing strategy that minimized left-turns in high-traffic zones. This approach led to over 10 million gallons of fuel saved annually and more than 100,000 metric tons of CO₂ eliminated. It demonstrates how operational efficiency and emissions reduction can be achieved simultaneously through fleet-level planning.
6. Implement Waste-to-Value Systems
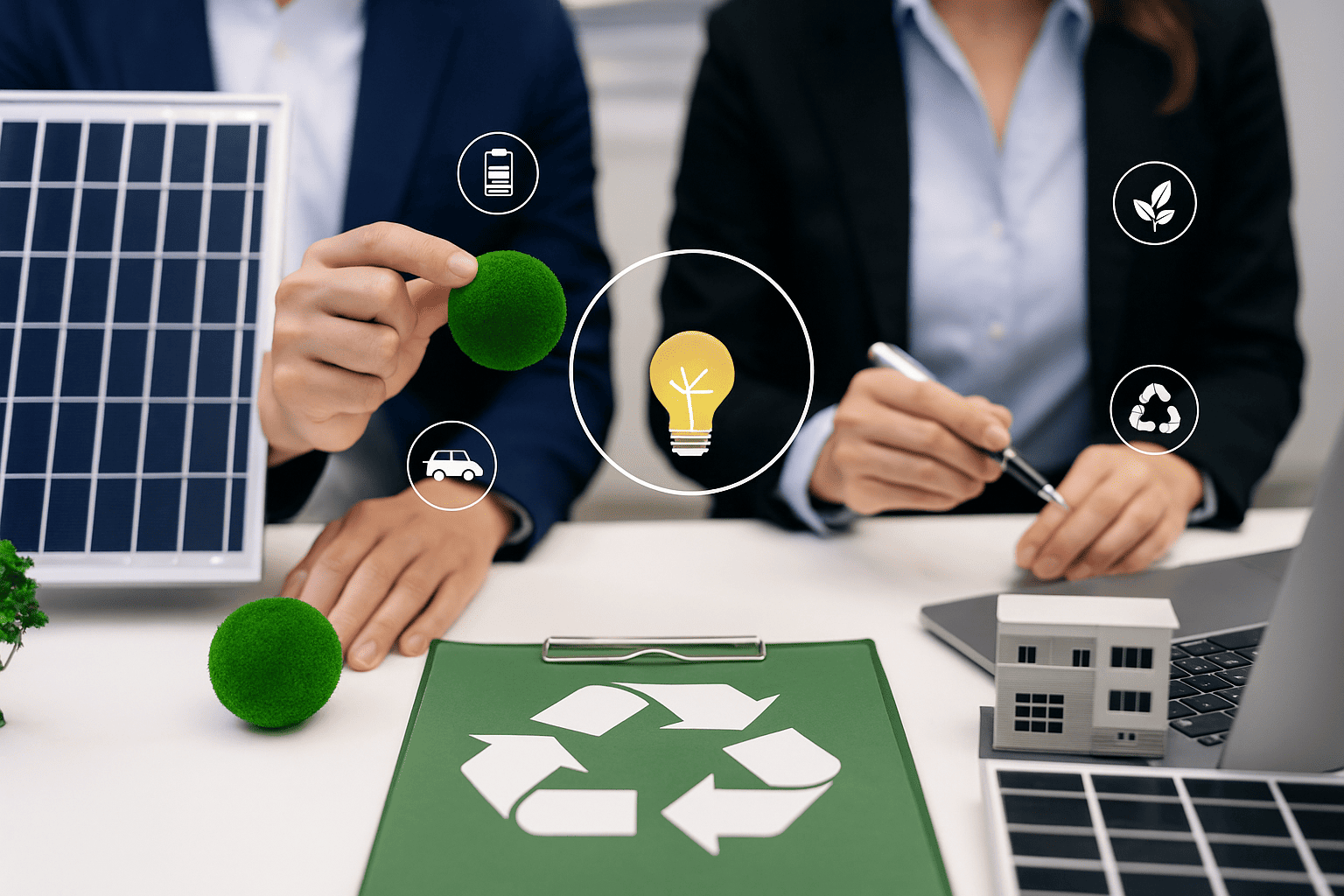
Manufacturing waste is often treated as a cost of doing business. But for asset-heavy organizations, it represents a strategic opportunity to recover value, reduce environmental risk, and improve material efficiency. Waste-to-value systems convert operational byproducts—such as organic waste, packaging residues, or metal scrap—into reusable inputs or secondary revenue streams.
These systems support landfill reduction, lower disposal costs, and improve compliance with increasingly stringent waste reporting requirements. They also allow organizations to extract residual value from materials that would otherwise contribute to environmental overhead.
As part of its manufacturing sustainability strategy, PepsiCo deployed a waste-to-energy system at its Portugal production facility. By converting over 20,000 tons of organic waste into biomethane annually, the company expects to reduce site-level emissions by 30%. The recovered energy offsets fossil fuel use in high-heat production processes—demonstrating how industrial-scale waste conversion can drive measurable environmental and operational gains.
7. Prioritize Green Procurement
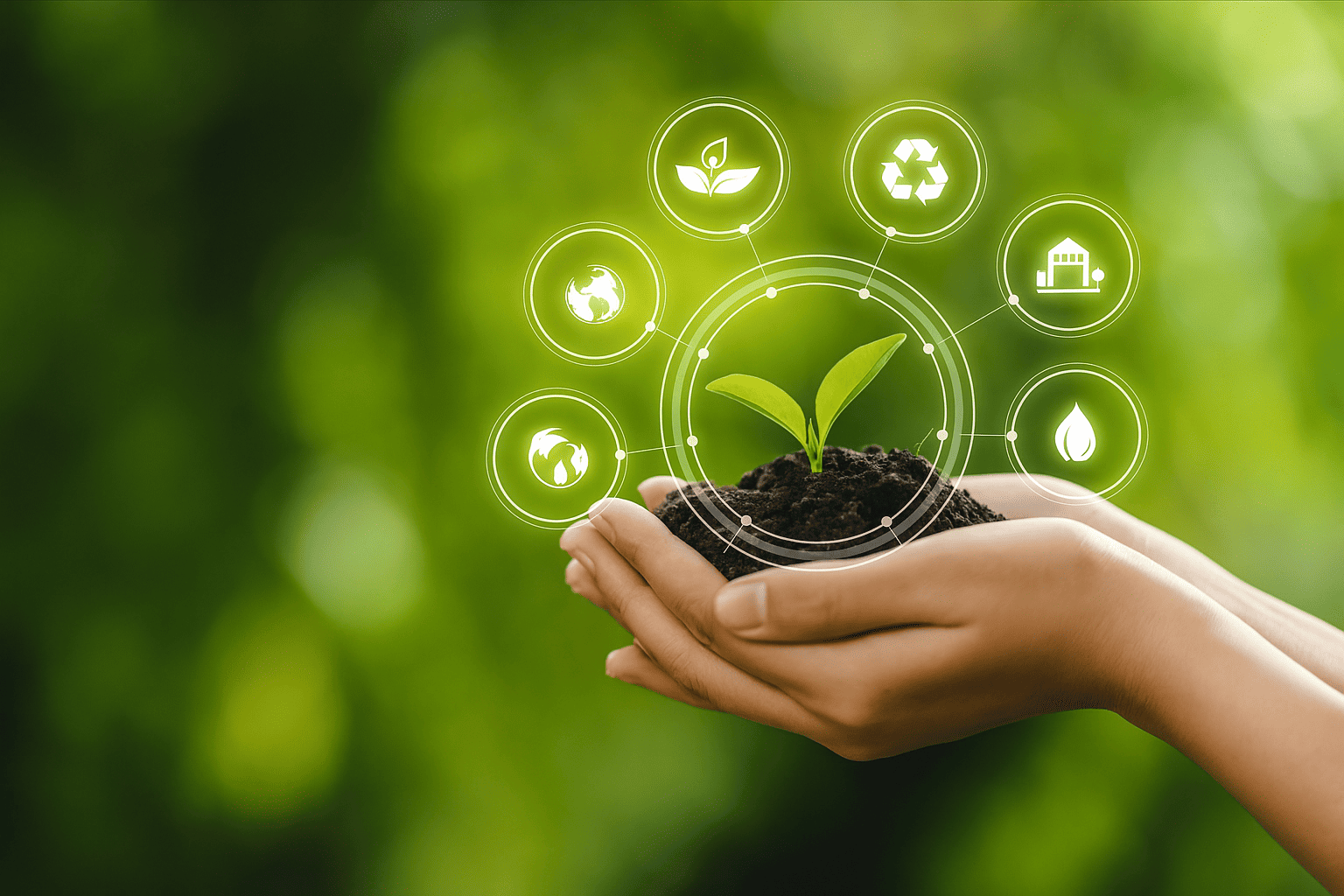
Procurement decisions have a direct impact on upstream emissions, resource efficiency, and supply chain resilience. For industrial organizations, sourcing from vendors that meet sustainability benchmarks strengthens environmental compliance and improves control over Scope 3 reporting.
Green procurement integrates defined ESG criteria into supplier qualification. This includes prioritizing materials with verified traceability, reduced embodied carbon, and lower packaging waste. These standards align sourcing activities with circular economy models and regulatory expectations.
Unilever, for example, embedded sustainability into procurement by increasing the visibility into its agricultural supply chain. The company prioritized suppliers based on environmental performance, traceability, and adherence to sustainable sourcing protocols, enabling it to drive measurable progress toward its goal of sourcing 100% of agricultural inputs sustainably.
8. Formalize Environmental Performance Tracking
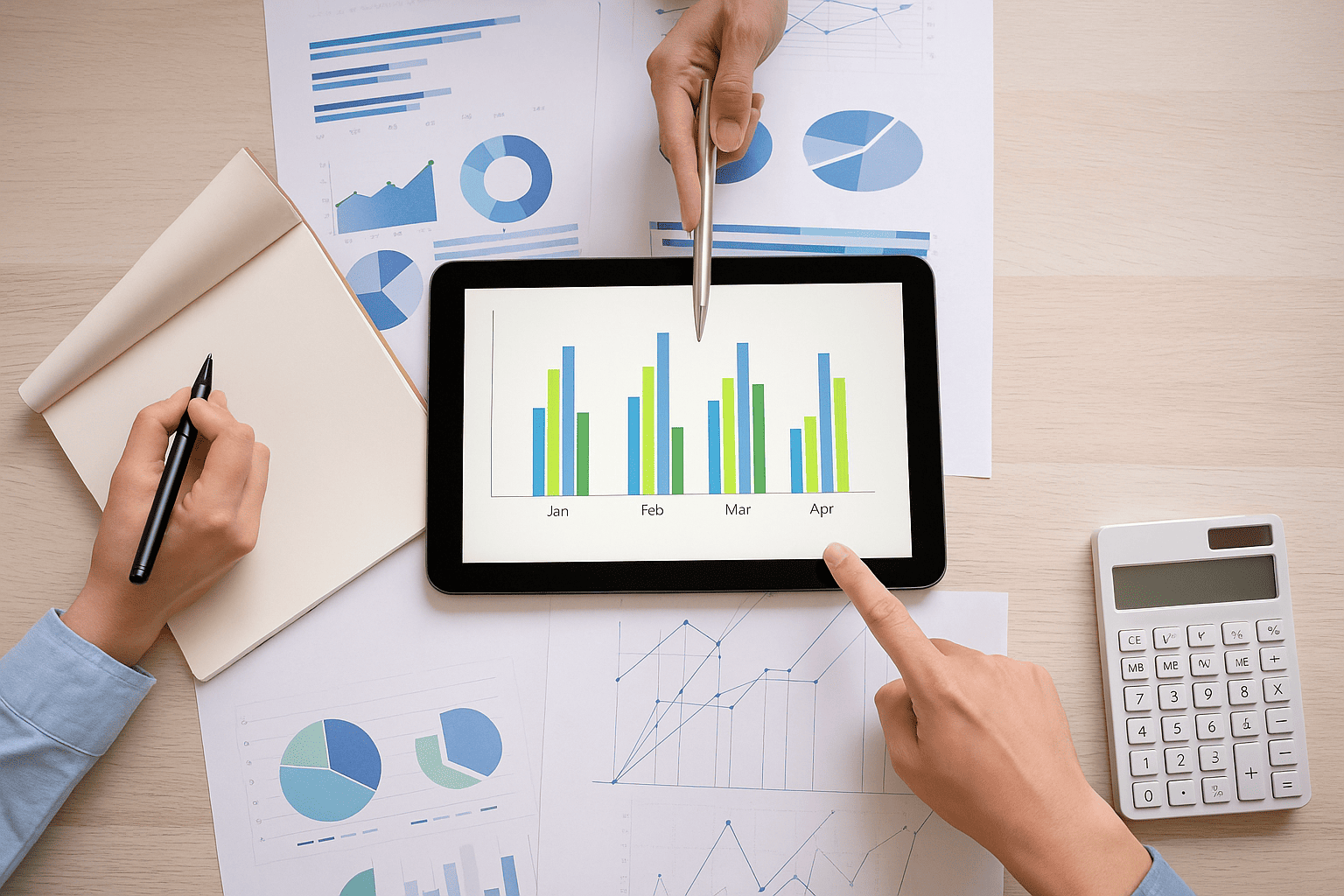
Environmental performance requires the same level of measurement discipline as cost or throughput. Manufacturers with formal sustainability mandates must establish structured KPIs—covering emissions, energy intensity, waste reduction, and resource recovery—to monitor progress and align with ESG frameworks.
Ford’s 2024 Integrated Sustainability and Financial Report reflects this approach at scale. The company consolidated its environmental and financial metrics into a unified reporting framework, tracking Scope 1 and 2 emissions, waste intensity, and energy usage across global operations. This integration enhances reporting accuracy, strengthens regulatory compliance, and ties sustainability targets directly to operational performance.
9. Engage Internal Teams with Incentive Programs
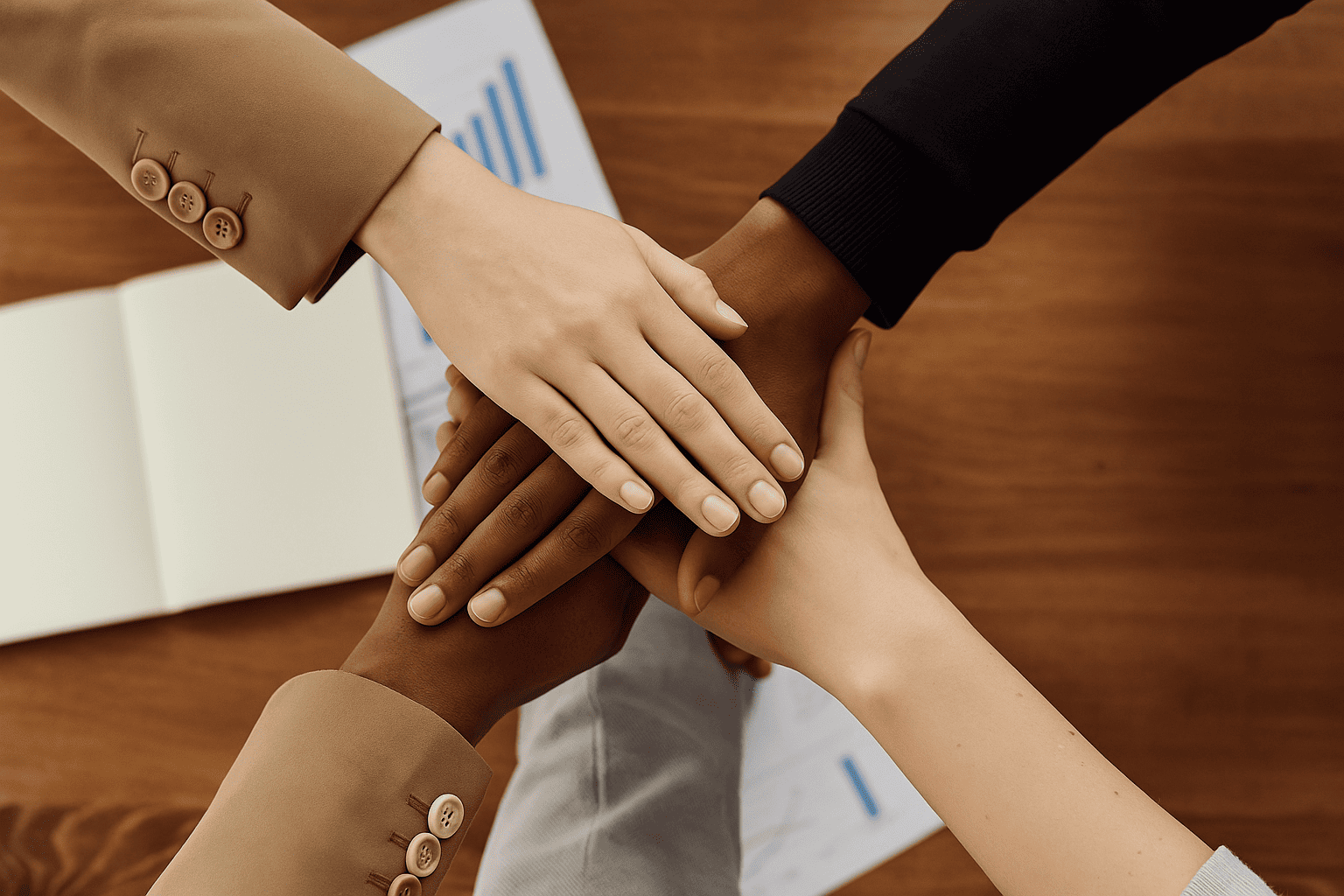
Operational behavior—equipment handling, shutdown routines, material usage—has a measurable impact on sustainable green outcomes. Without internal alignment, environmental initiatives remain isolated from day-to-day execution.
Leading manufacturers are addressing this by tying performance metrics to environmental targets. Structured incentives linked to energy reduction, resource recovery, or process efficiency drive behavioral change on the floor, not just in policy documents. Recognizing high-performing teams or sustainability champions reinforces accountability and continuous improvement.
3M operationalized this approach by embedding sustainability criteria into its Lean Six Sigma training, equipping more than 55,000 employees to identify and implement resource-saving process improvements. Its Pollution Prevention Pays (3P) program provided a framework for internal teams to contribute to emissions reduction and cost avoidance through formalized engagement.
10. Collaborate with Circular Economy Partners
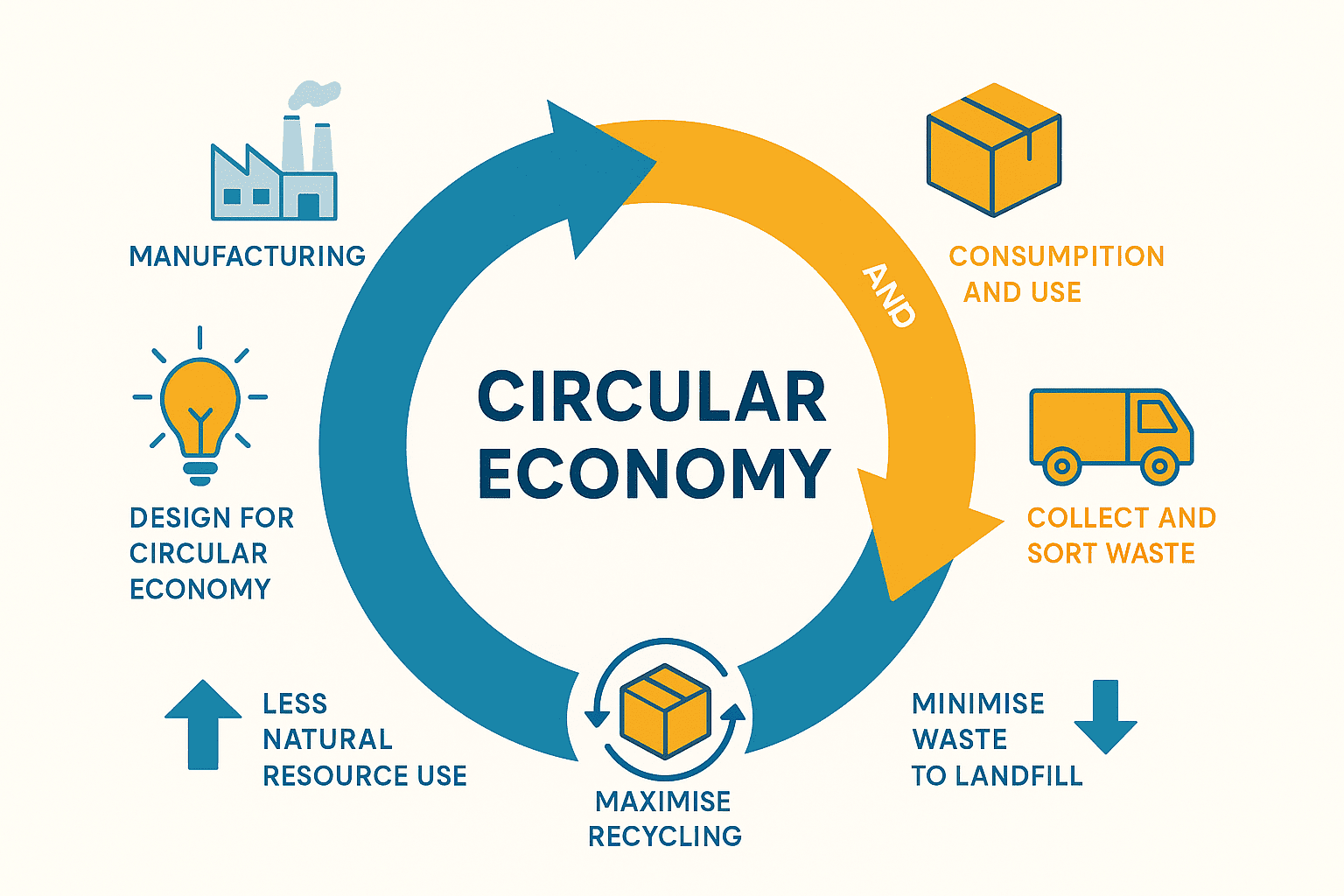
For industrial manufacturers, circular execution requires more than internal process control—it demands strategic alignment across sourcing, recovery, and lifecycle planning. Without that alignment, recovery value is lost, compliance risk increases, and material waste accumulates. External partnerships provide the scale and systems needed to extend industrial asset life and execute circularity at an operational level.
Amplio supported NCR Corporation during a component shortage that threatened a high-priority repair order. By sourcing 500 units of an Allegro MOSFET through trusted secondary channels, Amplio enabled NCR to maintain production timelines, meet quality standards, and avoid a $75,000 cost overrun. The engagement preserved system uptime and prevented early scrapping of repairable equipment, reinforcing circularity through supply-side continuity.
Conclusion
Green initiatives are no longer aspirational—they’re operational. For industrial manufacturers, integrating sustainability into core business functions improves efficiency, supports compliance, and strengthens financial performance. These outcomes are not theoretical. They begin with execution.
Amplio supports this shift by helping manufacturers execute controlled, compliant asset disposition—recovering value, reducing waste, and extending the productive life of equipment. These actions promote circular economy principles while improving operational and financial performance.
Connect with us to turn surplus industrial assets into a structured, sustainability-aligned recovery strategy.