Excess inventory can significantly undermine an enterprise’s financial agility and operational performance. According to NetSuite, carrying costs can account for up to 25% of the total inventory value. In practical terms, this means that for every $1 million of surplus stock, as much as $250,000 may be incurred in holding expenses. For industrial manufacturers, excess inventory is not merely a storage concern—it indicates a critical mismatch between production needs and procurement practices, leading to inefficient resource allocation and increased risk.
In today’s dynamic supply chain landscape, where operational pressures and global uncertainties are constant, understanding and managing excess inventory is paramount. Excess stock reduces the cash flow available for growth and innovation while disrupting efficient production by tying up vital capital in non-performing assets.
This blog will define excess inventory and detail its advantages and disadvantages. The insights presented here are designed to empower you to refine your procurement efficiency and improve overall business performance.
What Is Excess Inventory?
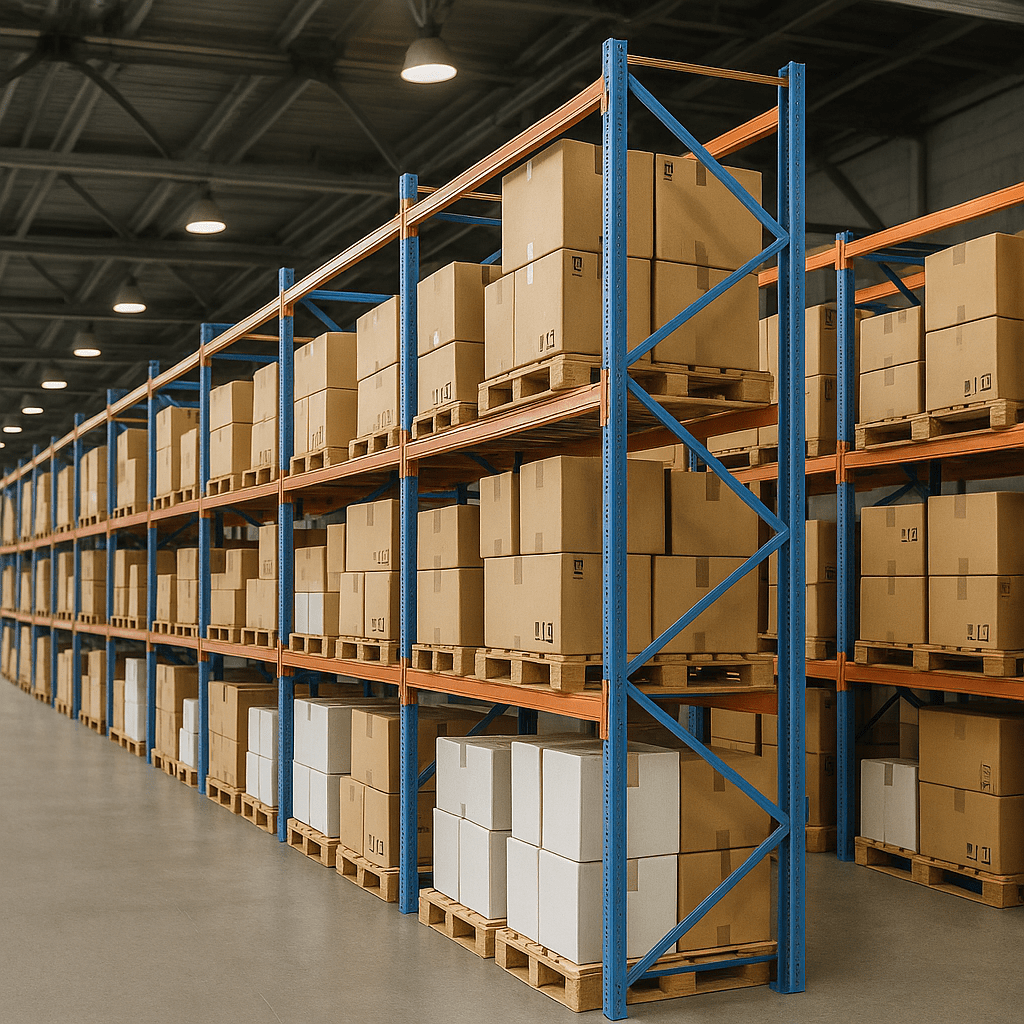
Excess inventory is the extra stock a business holds beyond its immediate or forecasted demand. It results when production or purchasing volumes exceed what the market and operation requires, typically due to overstocking, forecasting errors, or slow sales.
It is important to distinguish excess inventory from safety or buffer stock. Safety stock is deliberately maintained to cover demand fluctuations or supply disruptions. In contrast, excess inventory results from misaligned procurement strategy and inefficient planning. This discrepancy affects liquidity and operational performance, making it essential for you to manage inventory levels with precision.
Different Types of Excess Inventories
Excess inventory manifests in several distinct forms in industrial operations. Here are the various types:
- Overproduction Excess: Occurs when production volumes exceed the forecasted demand due to planning errors or overly aggressive capacity utilization. This type of surplus arises when the cost of underproduction is weighed higher than the risk of overproduction.
- Ordering Excess: Results from procurement practices that favor bulk purchases for volume discounts or to meet supplier minimums. This approach, aimed at short-term cost reduction, often leads to inventory levels that surpass actual operational requirements.
- Seasonal or Style-Related Excess: Develops in industries with cyclical demand or rapidly changing market trends. Overstocking during peak periods can leave manufacturers with inventory that loses value once demand shifts.
- Obsolescence Excess: This comprises items that are no longer required or have been phased out. These components rapidly lose their market and operational relevance, imposing financial strain as they occupy valuable storage space.
- MRO Inventory Excess: In some cases, maintenance, repair, and operations (MRO) inventory is held beyond what is necessary. While a certain level of MRO stock ensures smooth day-to-day operations, excess MRO items can create additional storage costs and tie up capital, highlighting a misalignment between stocking levels and actual usage.
What Is The Difference Between Excess and Surplus Inventory?
In enterprise manufacturing, the terms "excess" and "surplus" inventory are frequently used interchangeably but represent distinct concepts with important operational implications.
Excess inventory is extra stock that initially exceeds the needs of a particular site or department yet might be used elsewhere in the organization. In contrast, surplus inventory is any overstock that can no longer be redeployed internally and must be liquidated, donated, or discarded. Some experts also view surplus as an intentional or seasonal overage, while excess typically reflects unplanned overproduction.
A practical solution to managing unwanted industrial excess is excess inventory liquidation. By pursuing a structured asset recovery approach, you can convert unwanted inventory into working capital rather than incurring continuous holding costs.
Advantages of Excess Inventory
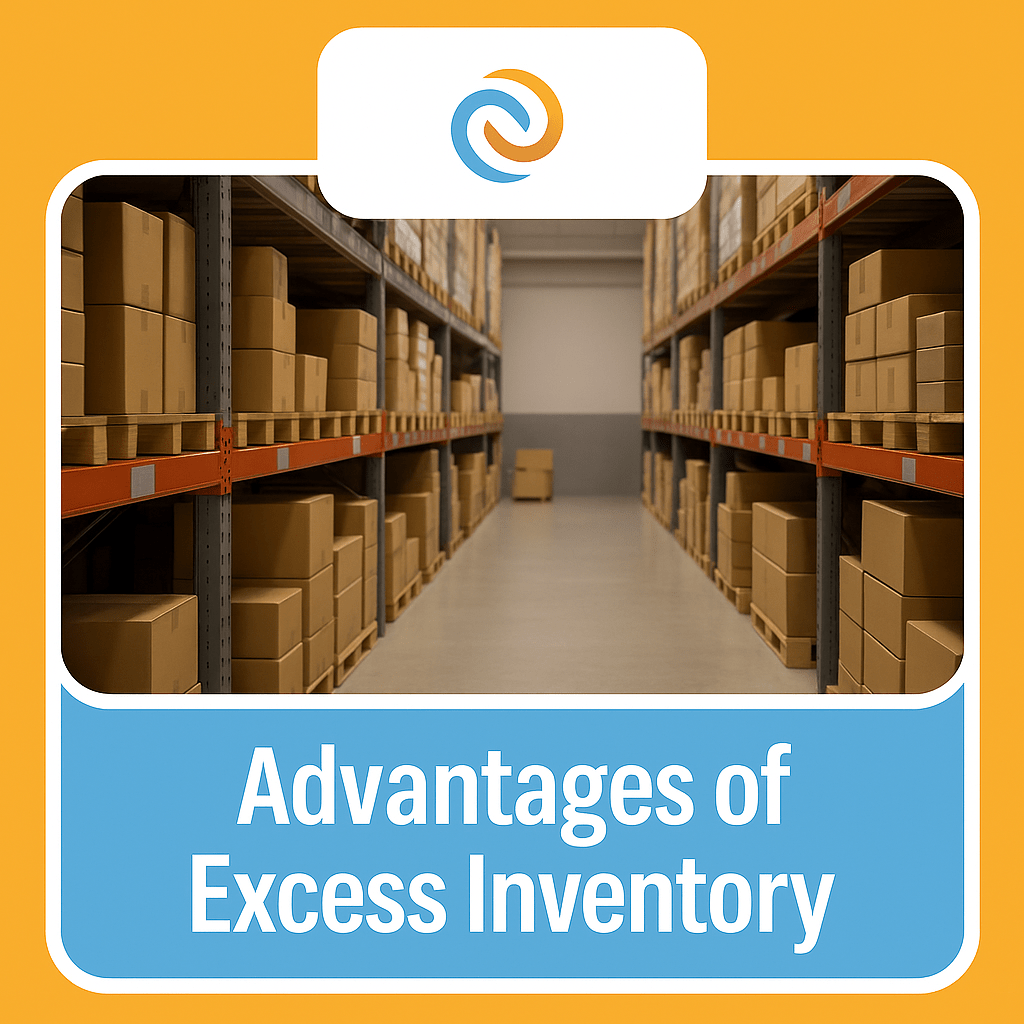
Below are the key advantages of managing excess inventory:
1. Buffer Against Demand Fluctuations
Excess inventory acts as a safeguard during unexpected spikes in demand. Maintaining additional stock on hand enables you to fulfill sudden orders and avoid stockouts. This buffer minimizes production delays and ensures that customer commitments are met even when market conditions change abruptly.
2. Bulk Purchasing and Cost Benefits
Over-ordering can yield significant financial advantages. When you purchase surplus inventory, you often secure volume discounts and lower unit costs. This approach strengthens supplier relationships in B2B contexts, contributing to a more efficient cost structure by reducing per-unit expenses over time.
3. Operational Continuity
A well-managed surplus ensures that your operations continue uninterrupted during supply chain disruptions. In the event of late shipments or raw material shortages, maintaining excess inventory helps you maintain steady production and safeguard revenue streams. In essence, having a controlled level of extra inventory provides a critical safety net that supports both operational stability and financial performance.
Disadvantages of Excess Inventory
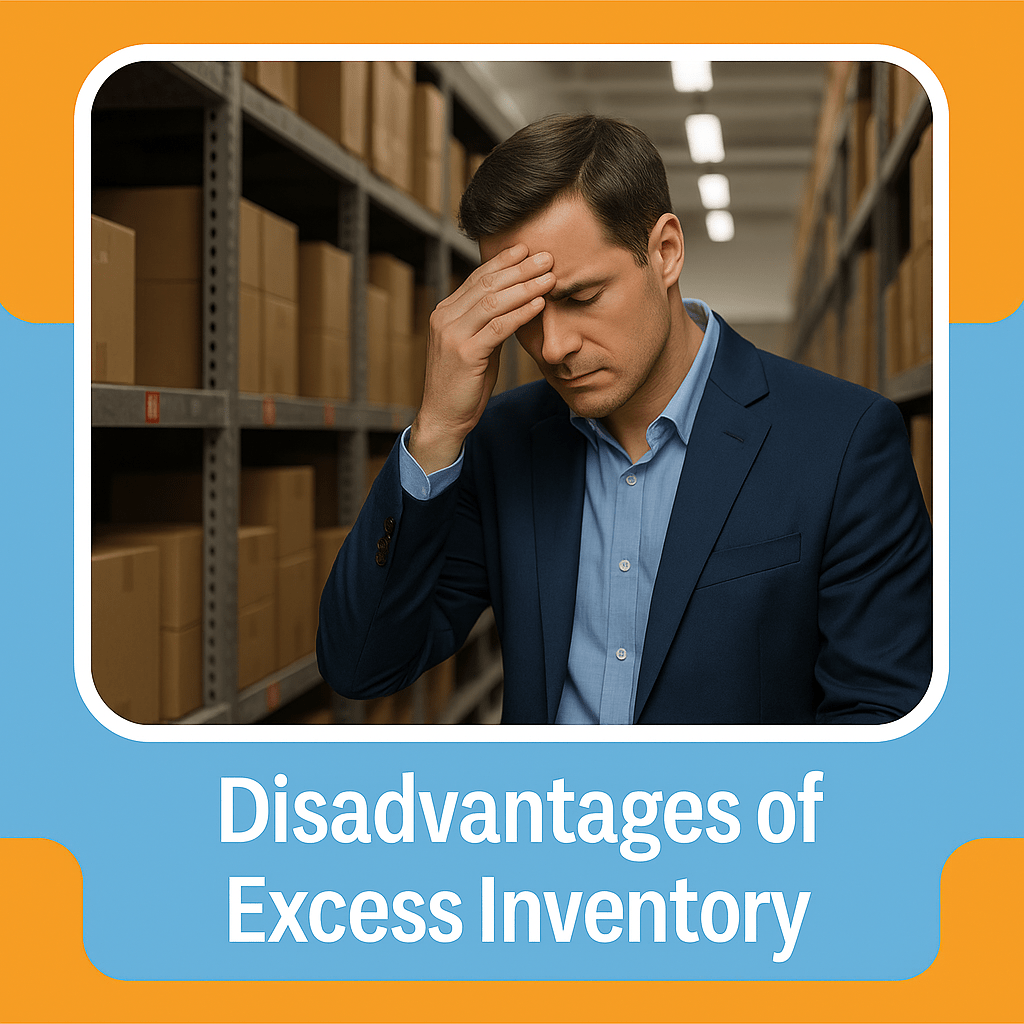
There are advantages to controlling excess inventory, but if it is not managed properly, it can lead to significant drawbacks. Below are the significant disadvantages and the consequences of carrying too much inventory:
1. Tied-Up Capital and Reduced Cash Flow
Excess inventory immobilizes a significant portion of your working capital, preventing it from being deployed for strategic initiatives or operational improvements. This locked capital diminishes your financial flexibility, forcing you to allocate funds to non-performing assets instead of growth opportunities. Consequently, the inability to invest in innovation or process optimization can further deteriorate your enterprise’s competitive position over time.
2. Higher Holding Costs
Carrying excess stock generates continuous expenses that add up over time, including warehouse rent, insurance premiums, and routine maintenance fees. These costs extend beyond the obvious financial outlay, impacting overall profitability as they divert resources that could be better allocated elsewhere. Moreover, managing higher inventory levels often requires additional labor and technology investments to maintain accurate tracking and efficient operations.
3. Obsolescence and Waste
Excess inventory can quickly become obsolete when product demand shifts, technology evolves, or market trends change, leaving you with items that lose their value rapidly. The depreciation of these outdated goods often forces companies to write down or dispose of unsellable stock, resulting in direct financial losses. Additionally, the process of disposing of or recycling obsolete inventory introduces further operational challenges and costs, disrupting smooth production schedules.
4. Complex Inventory Management
Handling excess inventory increases the complexity of your operations, as more stock requires enhanced tracking and management systems to avoid errors. With a larger volume of inventory, mismanagement becomes a risk, leading to inaccuracies in stock counts, increased administrative burdens, and potential shrinkage. This operational complexity can disrupt supply chain performance and necessitate additional investments in technology and training to maintain control and efficiency.
Final Thoughts
The advantages and disadvantages of excess industrial inventory highlight the critical need for disciplined inventory management in enterprise manufacturing.
Enterprise manufacturers should perform regular procurement audits and employ strategic inventory management practices to maintain optimal stock levels. Aligning your inventory with production requirements not only prevents waste but also safeguards your liquidity and operational agility.
To reduce inventory overhead, free up capital, and maintain a lean, resilient supply chain, consider industrial liquidation solutions. Amplio’s data-driven, compliant platform connects you with qualified buyers for your excess industrial equipment, offering a streamlined industrial liquidation solution.
Contact us today to drive efficiency and get rid of excess industrial inventory.