The global asset management system market is projected to grow from USD 17.64 billion in 2025 to USD 26.41 billion by 2030, at a CAGR of 8.4%. This growth reflects how industrial enterprises are prioritizing full-lifecycle asset control—from acquisition through to end-of-life decisions.
Within that lifecycle, asset disposition remains a critical unaddressed inflection point. Surplus equipment and idle machinery are not just operational inefficiencies—they represent tied-up capital, depreciating assets, and missed recovery opportunities. Unfortunately, asset management software and solutions often end where disposition begins, so the end of the asset lifecycle is not handled well.
This article looks to fill that gap by outlining the strategic value of structured asset disposition. It offers best practices designed to improve control, protect asset value, and support stronger operational and financial performance at scale.
What Is Asset Disposition?
Asset disposition refers to the structured process of managing assets at the end of their lifecycle. This includes the resale, redeployment, recycling, or disposal of equipment that no longer meets operational or financial requirements. It is a critical component of asset lifecycle management, ensuring that surplus or idle assets are removed in a controlled, compliant, and cost-effective manner.
For manufacturers and warehouse operators, disposition serves a specific objective in their suplus asset management approach. It enables the recovery of value from non-operating and unutilized tangible assets while reducing exposure, freeing up capacity, and maintaining operational control. Unlike informal disposal, it is guided by internal policy, financial targets, and regulatory standards.
Why Asset Disposition Matters for Industrial Businesses?
Idle equipment ties up working capital and reduces available floor space. As these assets sit unused, they continue to depreciate, incur storage costs, and limit operational flexibility. This creates a significant negative financial impact on asset-heavy environments.
According to the Investment Recovery Association, up to 10% of a large organization’s total assets can typically be classified as surplus or non-performing at any given time. This level of asset stagnation represents a measurable drag on both capital allocation and operational capacity.
Obsolete or underutilized machinery introduces additional risk. Equipment that no longer serves a production role may be outdated, non-compliant, or too costly to maintain. Retaining these assets delays reinvestment and creates inefficiencies across operations.
Without structured disposition management, asset turnover slows. Inventory remains misaligned with operational needs, and capital remains locked in assets that no longer generate value. Over time, this erodes productivity, increases exposure, and limits a business’s ability to scale efficiently.
Asset Disposition Methods
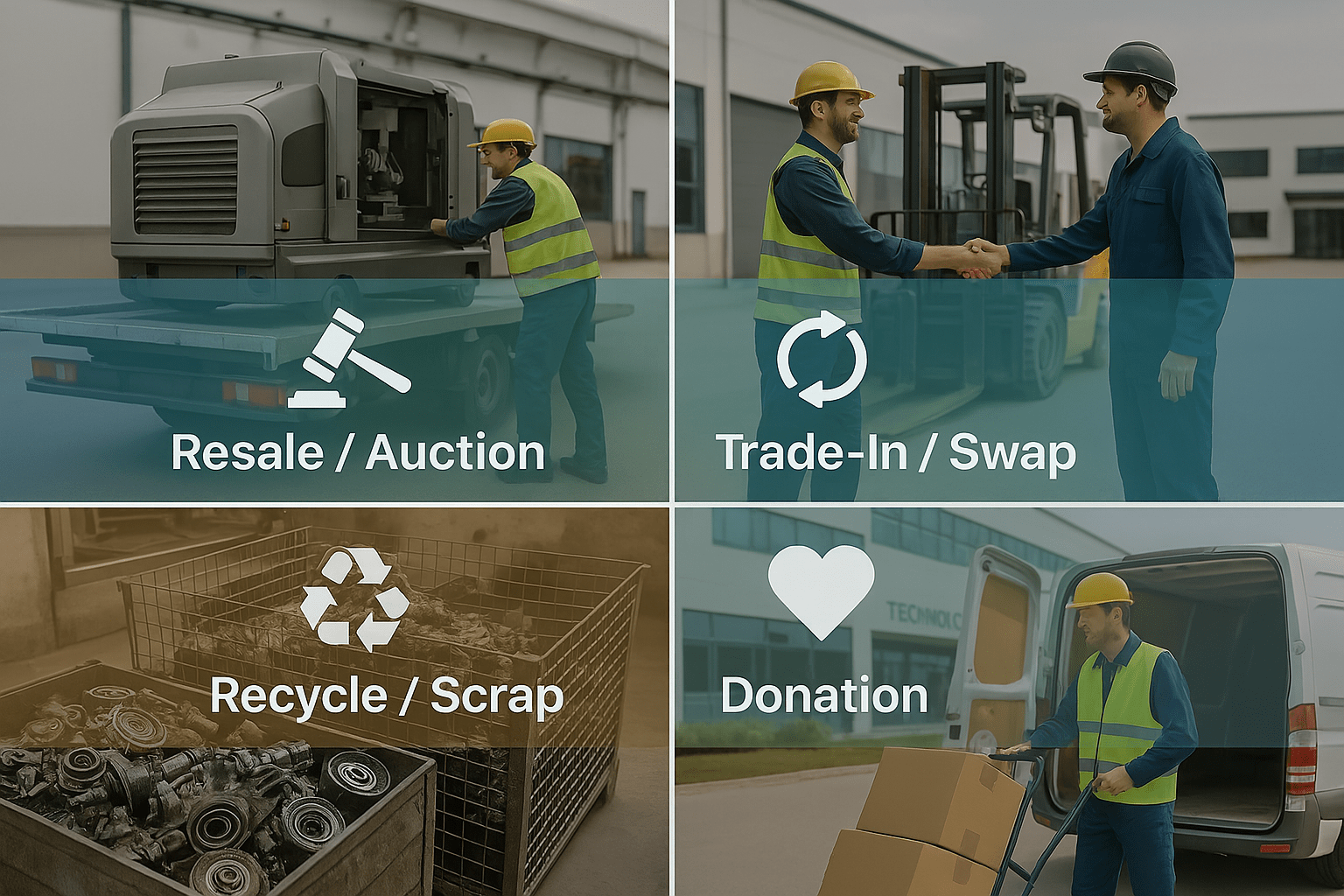
Industrial organizations have several options when removing surplus or underutilized equipment. Selecting the right method depends on the asset's condition, market value, internal policy, and compliance requirements. The following are the asset disposition methods commonly used in industrial environments:
- Resale or Auction
This method involves selling industrial surplus equipment through liquidation partners or specialized auction platforms. It is used when assets retain functional value and are marketable in secondary channels. It enables value recovery within a defined timeline, though outcomes depend on asset condition, pricing accuracy, and buyer interest.
- Trade-In or Equipment Swap
Trade-in programs allow businesses to exchange outdated assets when procuring new equipment, typically through OEMs or vendors. This reduces capital expenditure and eliminates the need for separate resale. It is limited to specific asset types and governed by vendor terms.
- Decommissioning, Recycling, or Scrapping
When equipment is obsolete, non-functional, or non-compliant, it must be removed through certified recycling or scrapping channels. This ensures regulatory adherence but typically yields minimal or no financial return and may require specialized handling.
- Donation
Functional surplus equipment may be donated to qualified nonprofit or educational institutions. This approach may offer tax benefits and support broader corporate responsibility goals. It requires strict documentation and must comply with asset transfer policies.
How to Build an Effective Disposition Strategy?
A disposition strategy must function as a defined component of the asset lifecycle—not as an afterthought. When aligned with lifecycle planning, it ensures that surplus or underperforming equipment is removed in a way that protects capital, maintains compliance, and supports operational continuity.
The following elements form the foundation of a controlled and effective disposition process:
- Accurate Asset Tracking and Reporting
Visibility begins with reliable data. Centralized tracking systems must provide detailed asset records, including location, status, usage history, and value. This enables early identification of idle equipment and supports informed decision-making at scale.
- Equipment Condition Grading
Each asset should be assessed based on operational condition, expected lifespan, and cost to maintain. Machinery and equipment appraisal helps standardize evaluation and ensures that disposition decisions are based on objective, repeatable criteria —particularly when determining whether to redeploy, sell, or retire the asset.
- Timelines and Market Timing
Timing has a direct impact on financial recovery. Disposition should account for both internal asset plans and external market conditions. Delays in removal reduce resale value and increase holding costs. A defined timeline aligned with market windows reduces loss and improves return on exit.
- Regulatory Compliance
Disposal must comply with environmental, safety, and industry-specific regulations. Whether retiring electronics, heavy machinery, or specialized equipment, processes must be documented and auditable. Non-compliance creates financial and legal risks that can be avoided with a structured, policy-aligned strategy.
Best Practices for Asset Disposition Management
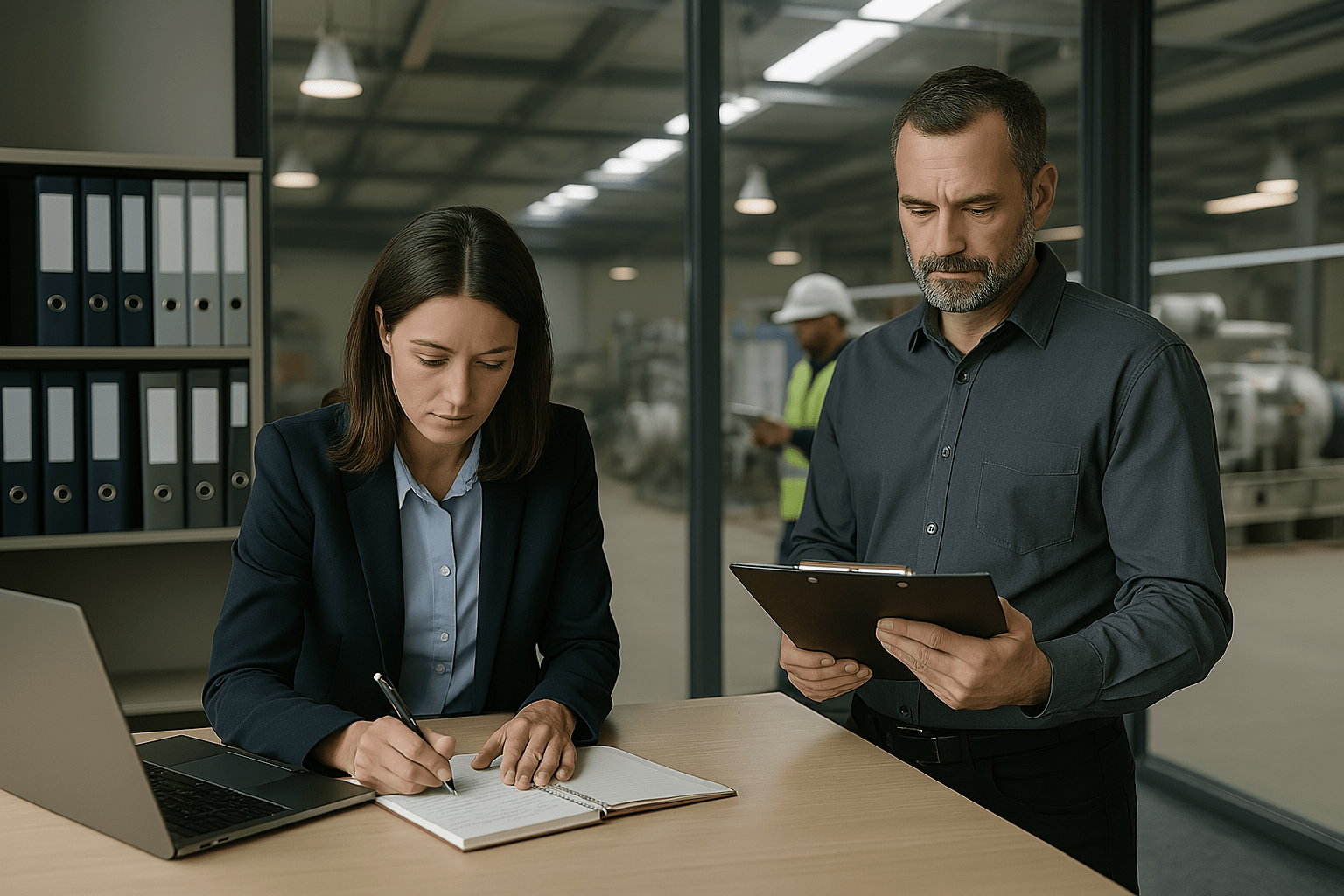
Asset disposition requires structure, control, and alignment with surplus asset management. The following practices form the foundation of an effective disposition framework.
- Centralized Asset Records
A unified asset register is essential. It must include real-time location, condition, ownership, and usage data across all sites. Without accurate records, identifying surplus equipment is delayed, increasing holding costs and creating inefficiencies. Centralized data also supports audit trails and internal governance protocols.
- Routine Asset Audits
Scheduled audits are necessary to determine which equipment is underutilized or no longer fit for purpose. This enables timely action before assets lose resale value or become non-compliant. Routine audits strengthen lifecycle oversight and reduce the likelihood of idle equipment remaining unaddressed.
- Independent Asset Valuation
Disposition decisions must be based on objective data. Equipment appraisals ensure that pricing reflects true market value and prevents internal bias from influencing asset recovery estimates. Independent appraisal also provides necessary documentation for audit, tax, and resale records.
- Market-Aligned Timing
Disposition timing should align with asset depreciation cycles and current market demand. Selling into a favorable market improves recovery value. Holding equipment beyond its economic life leads to unnecessary depreciation, increased storage costs, and reduced liquidity.
- Documentation and Recordkeeping
All disposition activity must be documented. This includes asset condition reports, valuation records, transfer documentation, and compliance forms. Documentation supports financial reporting, ensures tax alignment, and meets regulatory obligations, particularly in heavily regulated industries.
- ESG and Operational Efficiency Impact
Structured disposition contributes to ESG targets through recycling, reduced waste, and better resource utilization. Clearing non-performing assets improves space efficiency and supports leaner operations. These outcomes align with CSR commitments, internal KPIs, and long-term operational planning.
- Delegating Disposition to the Right Teams
In many industrial organizations, disposition responsibilities are informally assigned to procurement, despite falling outside their operational scope. This often leads to delayed decisions, unrealized recovery value, and increased compliance exposure. Where no formal investment recovery function exists, responsibility should shift to qualified specialists such as liquidation professionals, who manage disposition with market awareness, regulatory discipline, and a focus on maximizing asset value.
How Amplio Simplifies Asset Disposition for Industrial Sellers
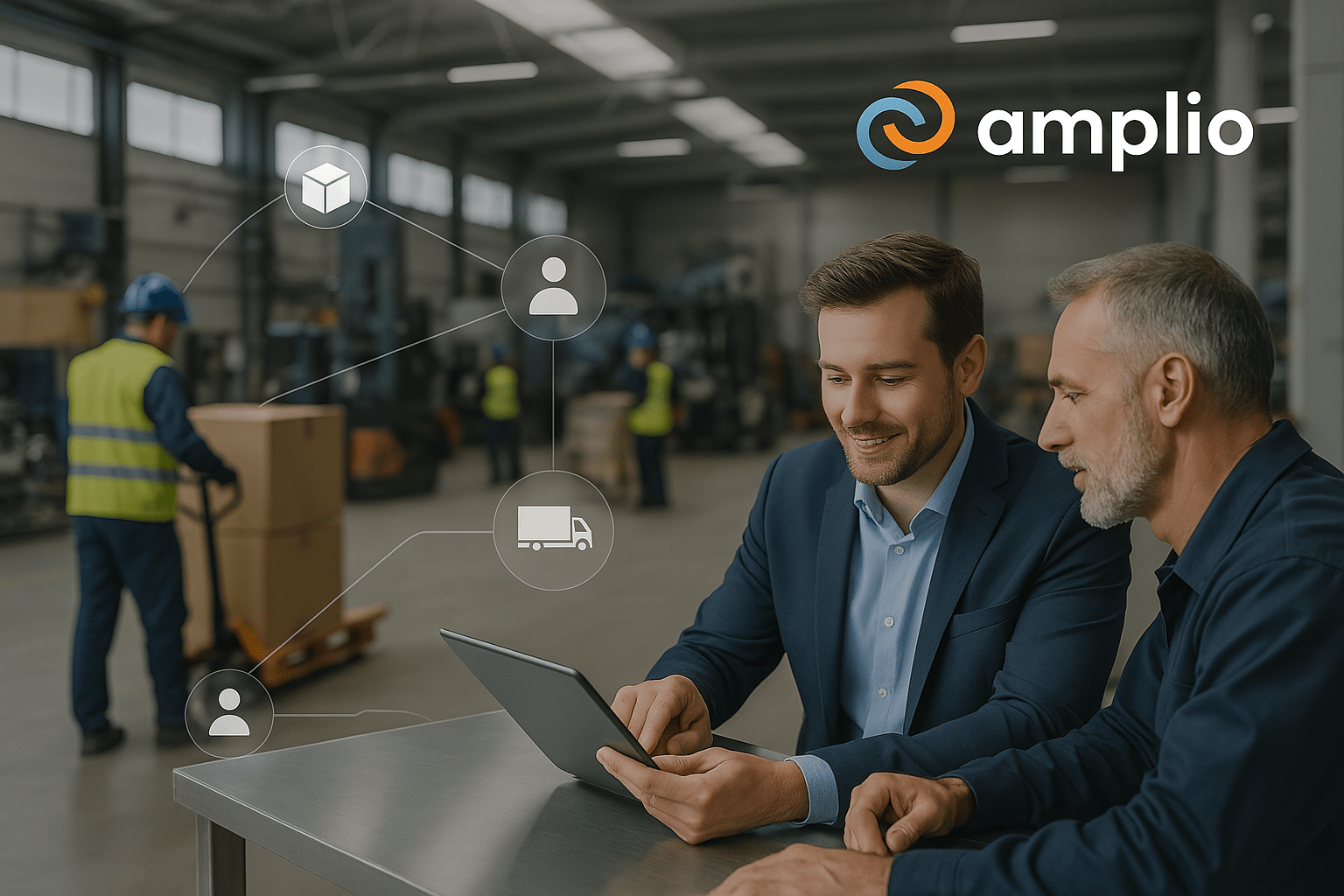
Amplio supports industrial organizations by turning disposition into a controlled, outcome-driven function. Rather than adding complexity or internal workload, our role is to remove friction from the asset exit process and deliver measurable business results. The value we provide extends well beyond transaction support – we’re a true turnkey solution that handles all aspects of asset disposition for our clients.
We reduce the resource drain typically associated with surplus equipment by streamlining the decision path from identification to removal. Sellers are connected directly to vetted industrial buyers, ensuring that assets reach the right market with minimal delay. This accelerates asset turnover and improves capital recovery.
Disposition events are documented in full alignment with audit and compliance requirements. Transparency is maintained throughout, enabling organizations to meet internal controls and regulatory obligations without disruption.
Amplio acts as a strategic partner in the disposition lifecycle, supporting financial clarity, operational agility, and enterprise-level liquidation-based disposition planning.
To explore a disposition strategy aligned with your business objectives, contact Amplio now.