The industrial machinery wholesaling industry in the United States is steadily growing, with a compound annual growth rate (CAGR) of 0.4% from 2019 to 2024. As businesses continuously upgrade equipment to remain competitive, older or surplus machinery frequently becomes idle or obsolete.
In this dynamic market, accurate appraisal of industrial machinery and equipment is critical, particularly for enterprises undergoing asset liquidation or restructuring. Precise valuations enable businesses to maximize recovery value, reduce financial risk, and strategically reinvest capital.
This blog explores key aspects of industrial machinery and equipment appraisal, covering valuation methods, influencing factors, challenges, and benefits to help businesses make informed decisions.
What is Industrial Machinery and Equipment Appraisal?
Industrial machinery and equipment appraisal is the process of evaluating the market value of a business’s operational assets, including machinery, equipment, and vehicles. These valuations are essential for financing, insurance coverage, and strategic asset management.
When is an Equipment Appraisal Necessary?
A commercial machinery appraisal is required in several business scenarios:
- Mergers & Acquisitions: Ensures accurate valuation of machinery assets during corporate transactions.
- Insurance Coverage: Determines the correct insured value, preventing underinsurance or excessive premiums.
- Taxation & Financial Reporting: Supports depreciation calculations and compliance with accounting standards.
- Asset Liquidation & Resale: Helps businesses recover maximum value from surplus or idle equipment.
- Collateral for Financing: Provides lenders with a reliable valuation of assets used in loan agreements.
Common Approaches to Industrial Equipment Appraisal
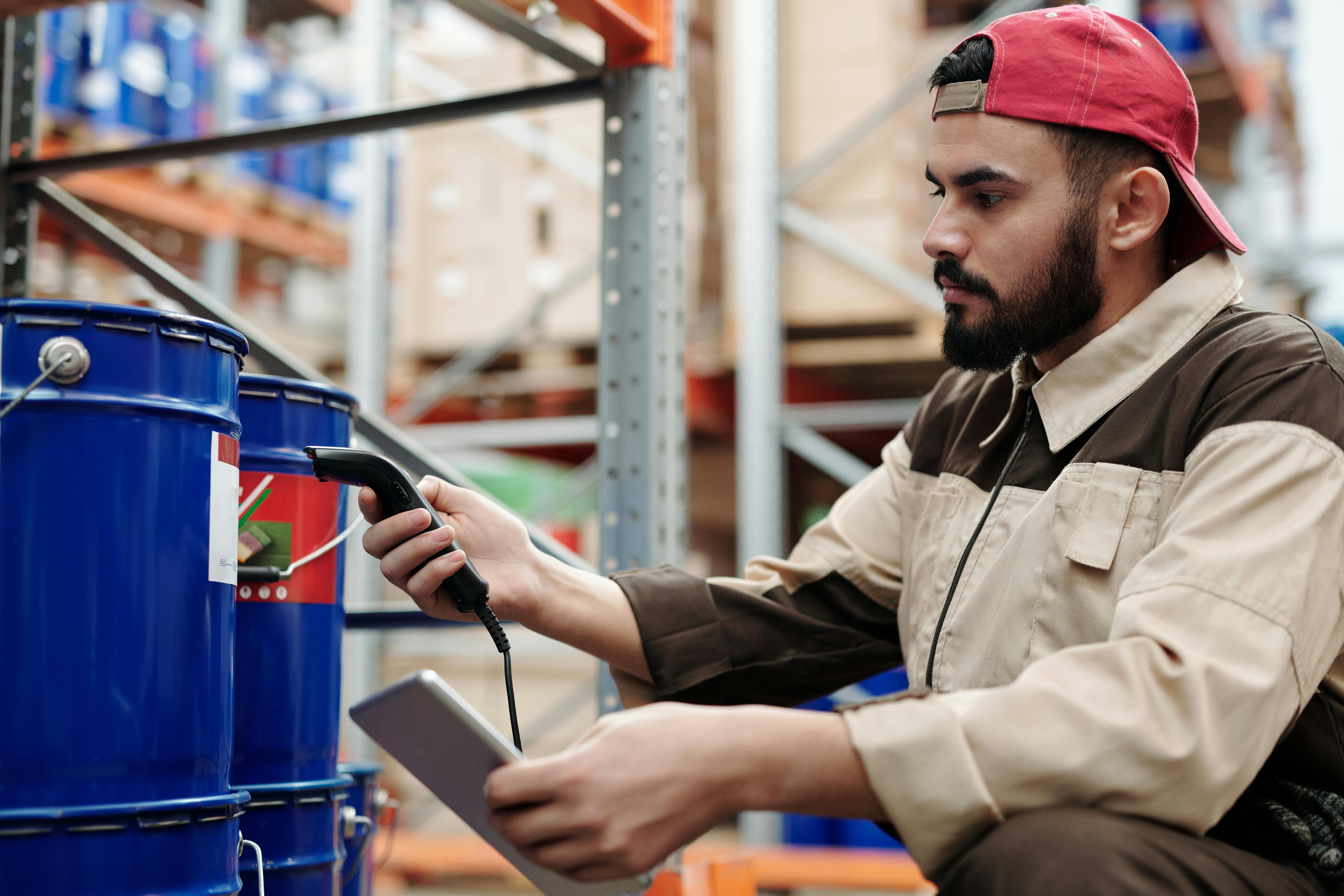
A structured valuation process is essential for determining the true market value of industrial machinery. In industrial machine appraisal, professionals use three primary valuation methods:
- Sales Comparison Approach
The sales comparison approach values machinery by comparing it to similar equipment recently sold in the market. This method relies on verified transaction data, considering factors such as:
- Age and condition of the machine
- Market demand and availability of comparables
- Industry-specific price fluctuations
This approach is widely used in industrial equipment appraisal for resale and liquidation purposes. However, its accuracy depends on the availability of comparable sales data. When market transactions are scarce, alternative valuation methods may be necessary.
- Income Approach
The income approach values equipment based on its ability to generate revenue or cost savings. This method is particularly relevant for assets that play a direct role in production efficiency and profitability.
Key factors in this approach include:
- Projected income from the machinery
- Operational efficiency and cost savings
- Depreciation over its useful life
For enterprises making capital investment decisions, the income approach provides insight into long-term financial returns, making it a valuable method for strategic asset planning.
- Cost Approach
The cost approach determines machinery value based on replacement or reproduction cost, adjusted for depreciation. This method calculates:
- Replacement Cost New (RCN): The cost of acquiring a new machine with similar capabilities.
- Reproduction Cost New (ReCN): The cost of manufacturing an identical machine.
- Depreciation Deductions: Adjustments for wear, obsolescence, and market shifts.
This approach is commonly used for insurance purposes, financial reporting, and tax assessments. It ensures that machinery is valued appropriately, reflecting both current market conditions and asset lifespan.
Factors Influencing Machinery Value
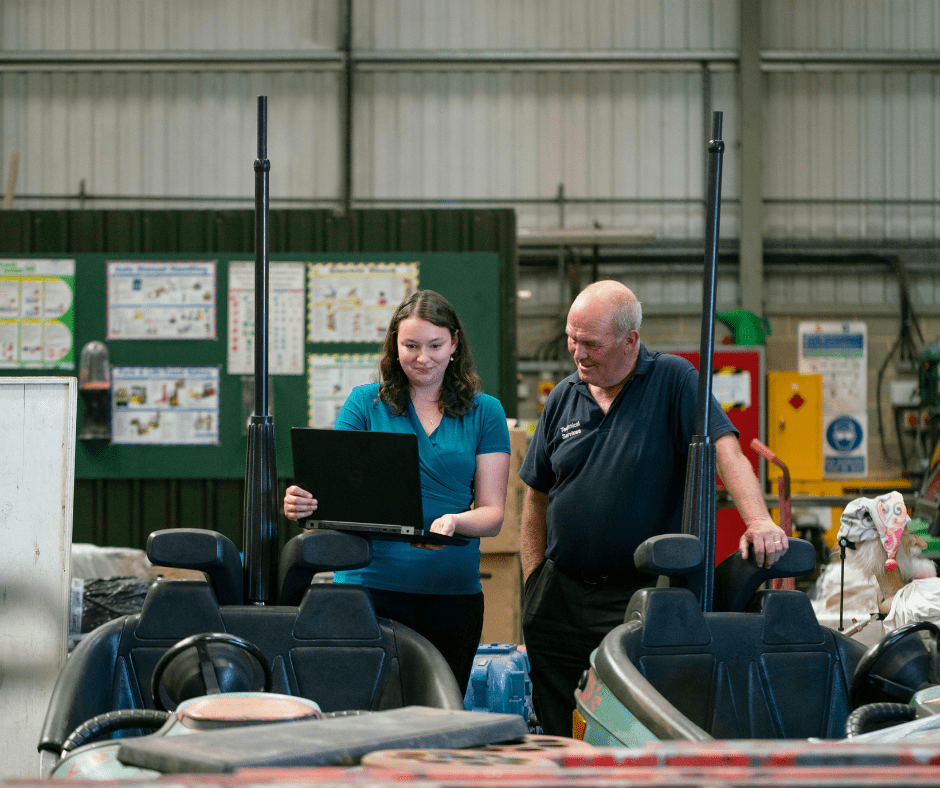
A precise industrial machine appraisal requires an in-depth evaluation of several factors that affect the asset’s financial worth. For enterprises managing high-value machinery, understanding these variables is essential for accurate financial reporting, insurance assessments, and asset value recovery.
- Age and Condition
The operational lifespan and physical condition of machinery play a crucial role in its valuation. Equipment that is well-maintained, fully functional, and free from excessive wear holds its value better. Conversely, machinery with significant deterioration, outdated components, or mechanical failures depreciates quickly.
- Technological Relevance
As industries adopt automation, data-driven manufacturing, and energy-efficient solutions, older machines may become obsolete. Equipment that integrates modern technology and meets current production standards is valued higher. Machinery without upgradable software, compatible interfaces, or compliance with new regulations sees a sharp decline in market demand.
- Market Demand
The availability and demand for specific machinery directly impact its appraisal value. In high-demand industries, machines retain value due to limited supply and production needs. However, when newer, more efficient models enter the market, older equipment may experience depreciation. Industry shifts, global supply chain disruptions, and economic conditions also influence resale potential.
- Maintenance and Repair History
A detailed maintenance and repair history is critical in determining equipment value. Machinery with documented service records, routine inspections, and minimal downtime holds greater resale and operational worth. Buyers and appraisers assess:
- Preventative maintenance schedules
- OEM part replacements vs. aftermarket modifications
- Equipment downtime and major repairs
The Appraisal Process
A structured industrial machine appraisal ensures enterprises receive an accurate valuation of their assets. This process involves four key steps, each designed to provide a comprehensive assessment while ensuring compliance with financial, regulatory, and operational standards.
- Initial Consultation
The appraisal process begins with a strategic consultation to define objectives and establish the appraisal framework. This step includes:
- Purpose of the appraisal—financial reporting, insurance coverage, taxation, or liquidation.
- Scope of assessment—type, number, and condition of the machines under evaluation.
- Industry standards and compliance requirements that must be met.
- Timeline for completion and delivery of the final report.
A well-defined appraisal scope ensures that businesses receive a valuation customized to their operational and financial needs.
- Data Collection
Comprehensive data collection is critical for an accurate industrial equipment appraisal. This involves gathering:
- Manufacturer specifications—make, model, serial number, and production year.
- Operational usage history—hours of operation, workload capacity, and performance records.
- Maintenance and repair logs—service schedules, parts replacements, and upgrades.
- Modifications or enhancements—any changes that affect performance, efficiency, or compliance.
A detailed equipment history strengthens the appraisal process by providing insights into asset longevity, depreciation, and market positioning.
- Inspection
A physical inspection is conducted to verify the condition and functionality of the machinery. This assessment includes:
- Structural and mechanical integrity—wear, corrosion, and overall performance.
- Operational efficiency—output capacity, automation levels, and software compatibility.
- Compliance with industry standards—safety, environmental, and regulatory considerations.
For a manufacturing equipment appraisal, this step provides a real-world assessment of how an asset performs, ensuring that the valuation reflects actual market value.
- Analysis and Report Generation
The final step involves applying valuation methodologies to determine the fair market value of the equipment. The appraisal report includes:
- Valuation conclusions based on the Sales Comparison, Income, or Cost Approach.
- Depreciation analysis and projected remaining useful life.
- Market conditions and resale potential insights.
Common Challenges in Machinery Appraisal
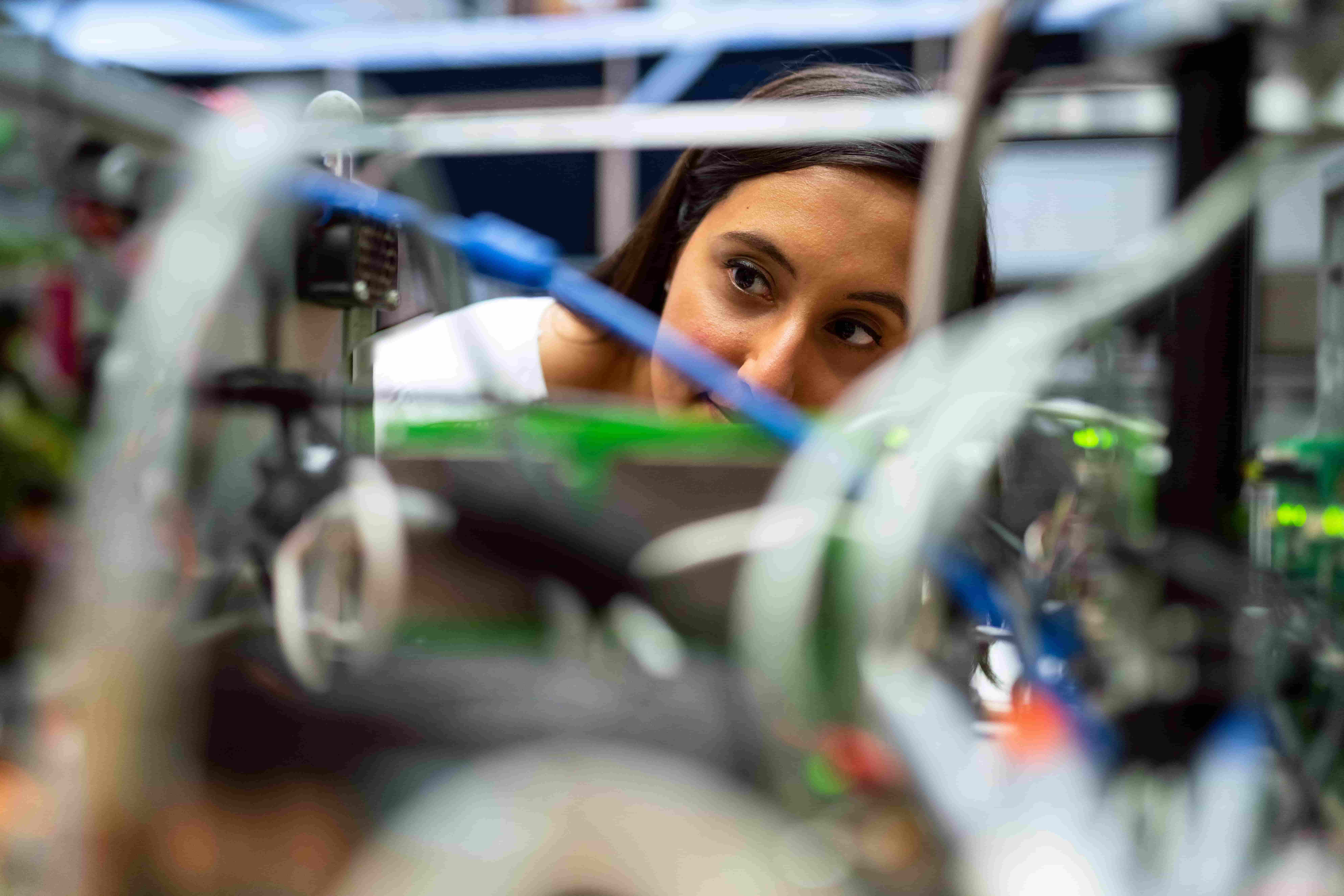
Despite the structured approach to industrial machine appraisal, several challenges can impact valuation accuracy and reliability. Enterprises must navigate these complexities to ensure their machinery and equipment appraisal aligns with market realities and financial objectives.
1. Limited Market Comparables
Valuing specialized or custom-built machinery can be difficult due to limited transaction history and unique configurations. Unlike widely traded equipment, these assets may lack direct market comparisons, requiring appraisers to use alternative valuation models that can introduce variability in pricing.
2. Rapid Technological Advancements
The pace of automation and technological innovation shortens the lifecycle of industrial machinery. Once cutting-edge equipment may quickly become outdated, affecting both operational efficiency and resale value. Businesses must assess whether their assets still align with current industry standards or have been impacted by technological shifts.
3. Fluctuating Market Conditions
Machinery values are directly influenced by economic cycles, supply chain disruptions, and industry demand shifts. Rising raw material costs, evolving trade policies, and geopolitical uncertainties can cause unpredictable fluctuations in resale pricing. Enterprises must continuously monitor these external factors to ensure their asset valuations remain relevant.
4. Variability in Condition Assessments
A machine’s physical condition, maintenance history, and wear significantly impact its value. However, appraisers may evaluate these factors differently, leading to inconsistent valuation results. Without a standardized condition grading system, businesses may receive varied assessments for the same equipment.
5. Lack of Standardized Valuation Methods
Industrial machinery does not always have a universal valuation benchmark, especially for highly specialized or obsolete equipment. Different appraisers may prioritize cost, market, or income-based approaches, leading to discrepancies in final valuations. Enterprises must ensure their commercial machinery appraisal follows an appropriate and consistent methodology to maintain financial accuracy.
Why Appraisals Are Important
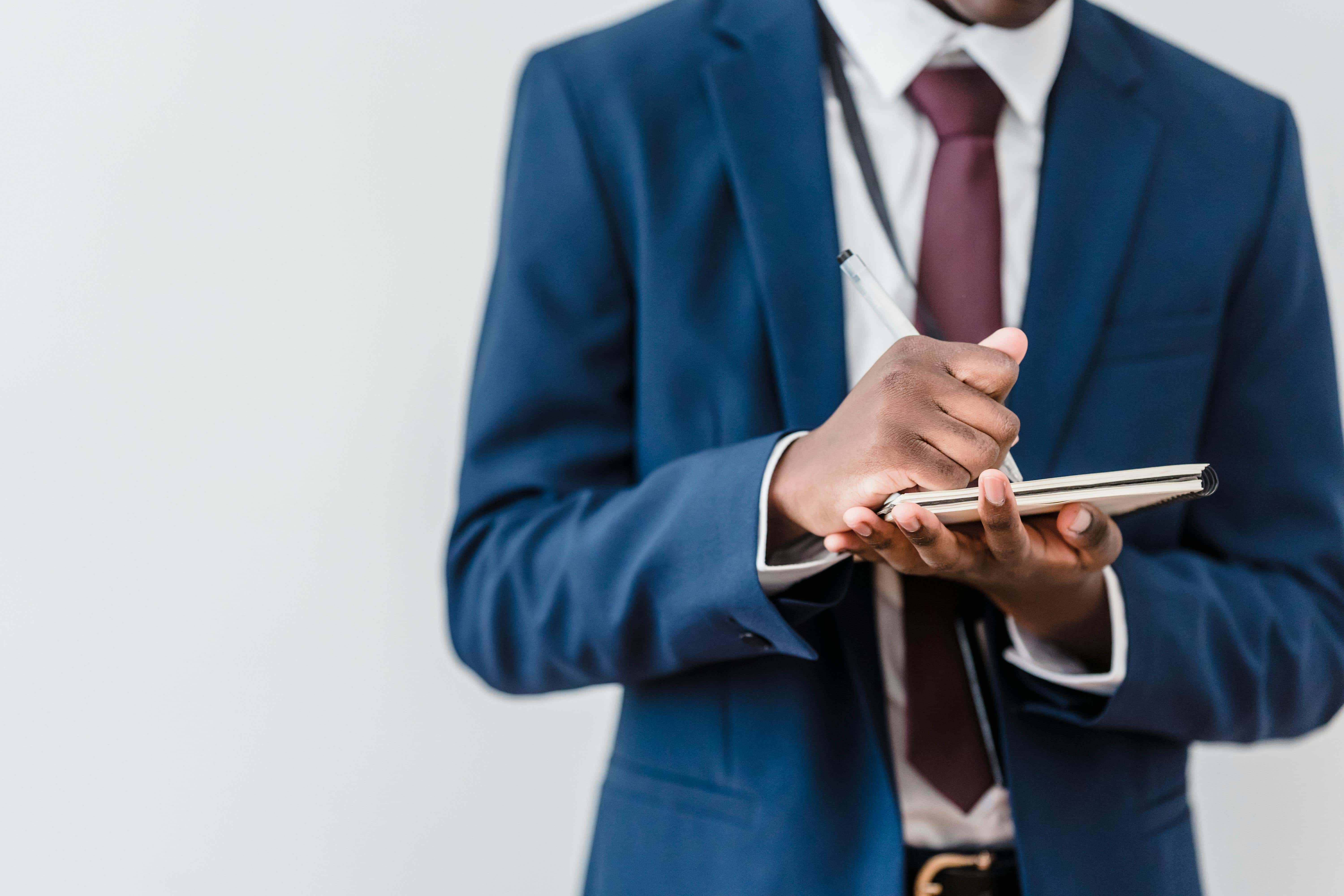
Accurate industrial machine appraisal is essential for enterprises managing high-value assets. A precise valuation ensures compliance, financial transparency, and strategic decision-making.
Here are the key benefits:
1. Financial Compliance and Reporting
Proper machinery and equipment appraisal ensures compliance with accounting regulations and tax filings. It prevents financial misstatements and supports accurate audit reporting.
2. Improved Asset Management
Enterprises use industrial equipment appraisal to track depreciation and optimize capital investments. Accurate valuations help in planning equipment upgrades and replacements.
3. Insurance Risk Mitigation
A commercial machinery appraisal determines the correct replacement cost of assets. It ensures businesses have adequate coverage while avoiding overinsurance or underinsurance.
4. Maximized Resale and Liquidation Value
Precise valuation supports better pricing strategies for surplus asset sales. It helps enterprises secure optimal returns when liquidating machinery.
5. Enhanced Financing and Lending Opportunities
A manufacturing equipment appraisal provides lenders with verified asset values. This supports loan approvals, asset-backed lending, and improved financing terms.
How Does Amplio Provide Machinery and Equipment Appraisals as Part of the Liquidation Process?
Amplio integrates machinery and equipment appraisals into its structured industrial asset liquidation process, ensuring sellers receive accurate, data-driven valuations as part of a seamless transaction. Our appraisal service is designed to support optimal pricing and market-aligned decision-making, allowing businesses to maximize asset recovery. We don’t offer appraisals as a stand-alone service; we execute it as part of our broader capability to solve surplus asset challenges for our clients.
By utilizing real-time secondary market insights and industry benchmarks, Amplio determines the fair market value of machinery based on condition, demand, and depreciation trends. This ensures transparency and precision in pricing assets for sale, helping us achieve the best possible return for our clients.
For buyers seeking reliable industrial equipment, Amplio provides access to pre-vetted machinery with verified appraisals, ensuring quality and competitive pricing.
Get started with Amplio for a streamlined, data-backed liquidation process that includes professional machinery appraisals and maximized asset value.