According to 2024 survey data from Warehousing and Fulfillment, the yearly cost per square foot for warehouse storage was $8.31 in 2024. For a 100,000‑square‑foot facility storing surplus equipment, this resulted in an annual cost of approximately $831,000 in 2024 compared to $796,000 in 2022.
With rising warehouse costs for owners, idle inventory has become a growing challenge for manufacturers of all sizes. When inventory sits unused, it takes up valuable space, ties up working capital, and impacts cash flow and operational efficiency.
For manufacturers, effectively managing idle inventory is essential to reclaiming space, reducing expenses, and optimizing operations. This guide explores what idle inventory is, its impact on businesses, and the best strategies to manage it efficiently.
What Is Idle Inventory?
Idle inventory refers to stock that remains unsold or unused for an extended period, taking up valuable warehouse space without contributing to revenue. Unlike regularly moving inventory, idle inventory sits stagnant, tying up capital and increasing storage costs.
For enterprise manufacturers, idle inventory often includes surplus raw materials, unused electronics, obsolete spare parts, or finished goods that no longer align with operations, production schedules or market demand.
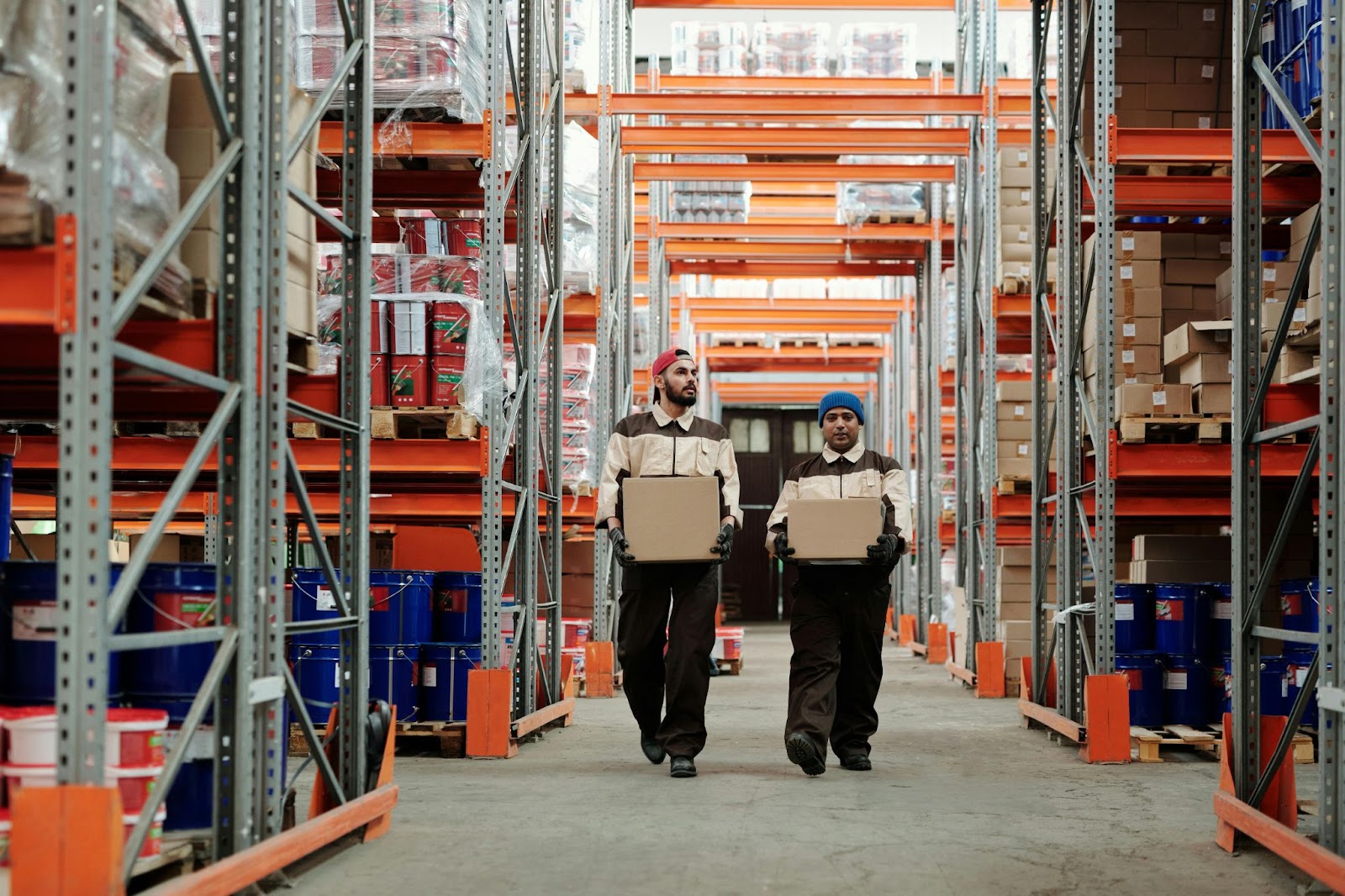
Categories of Idle Inventory
Idle inventory exists in various forms, each impacting cash flow, warehouse efficiency, and overall operations differently. Here are the most common types:
1. Overstock
Overstock refers to excess inventory resulting from overproduction or inaccurate demand forecasting. For example, if a manufacturer orders too many raw materials expecting higher demand, the surplus becomes overstock, tying up capital and warehouse space.
2. Obsolete Inventory
Obsoletes stock refers to idle equipment that has lost its market value due to technological advancements or industry shifts. Outdated machine components that are no longer compatible with newer equipment are a common example.
3. Slow-Moving Stock
Slow-moving stocks are products with minimal turnover accumulated over time. These items, such as rarely used spare parts, remain in storage for extended periods.
4. Seasonal/Cyclical Inventory
Seasonal items refer to products that experience demand only during specific periods. They may sell quickly during peak seasons but remain idle during off-peak times, creating storage challenges and inefficiencies.
5. Damaged Stock
As the name indicates it refers to stock that has been physically damaged or degraded, making it unsellable or difficult to use. Industrial parts that are mishandled during transit or returned in poor condition contribute to this category.
Causes of Idle Inventory
Here are the common causes of idle equipment and inventory that manufacturers encounter:
1. Misjudged Demand Forecasts
When demand forecasts are overly optimistic, companies produce or order more raw materials than the market requires. This disconnect between anticipated and actual demand results in an accumulation of inventory. Often, shifts in market conditions or economic factors contribute to this miscalculation, emphasizing the need for more precise forecasting methods.
2. Supply Chain Disruptions
Interruptions in the supply chain such as delays in raw material deliveries, logistical bottlenecks, or external geopolitical issues can misalign production schedules with market demand. These disruptions lead to situations where inventory remains idle because production plans cannot be adjusted in time.
3. Equipment Obsolescence
Another significant cause is the rapid technological advances, procurement of new machinery, and evolving industry standards that can render certain MRO equipment or components outdated. When new technologies emerge, older inventory may quickly lose its relevance, resulting in stock that no longer serves operational needs.
4. Lack of Inventory Visibility
While not always a major cause, siloed data and outdated tracking systems can make it difficult to maintain accurate inventory records, leading to duplicate orders, misplaced stock, and unnecessary accumulation of idle inventory. Without full visibility across warehouses and production sites, manufacturers may unknowingly overorder materials. For example, a manufacturer might purchase additional bolts for production because its ERP system fails to flag existing stock in a remote warehouse.
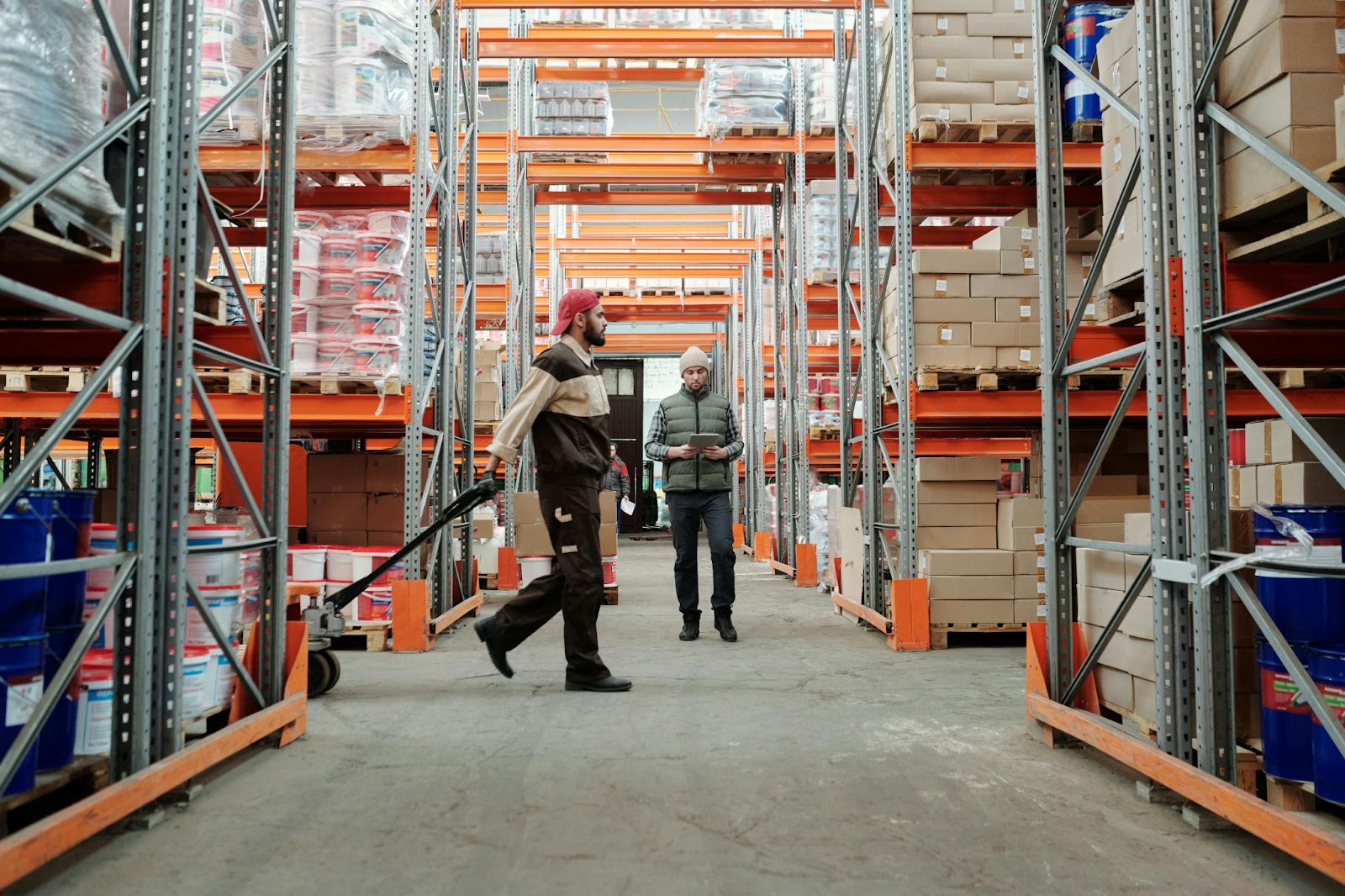
Impacts of Idle Inventory on Your Business
Understanding the causes of idle inventory is only part of the equation. The real challenge lies in the financial and operational impact it has on manufacturers. When inventory sits idle, it creates inefficiencies that extend beyond storage, affecting capital allocation, overhead costs, and long-term profitability.
1. CAPEX Cost
Idle inventory ties up capital that could be invested in new equipment, technology upgrades, or production improvements. When funds remain locked in unsold or unused stock, businesses face reduced flexibility in allocating capital expenditures (CAPEX) toward innovation and expansion. Instead of fueling growth, these idle resources remain stagnant, limiting a company's ability to respond to market demands.
2. Increased Overhead Costs
Idle inventory requires ongoing management, leading to higher costs for security, storage, insurance, and labor. The longer products remain in storage, the more they drive up operational expenses. Carrying costs for inventory typically average around 21% of its original asset value per year, meaning that for every year a piece of equipment remains unsold, a manufacturer incurs 21% of its value in overhead expenses. For example, storing a $100 pump costs $21 annually, and over time, these accumulating costs can surpass the item's recoverable value, turning idle inventory into a financial liability.
3. Reduced Warehouse Efficiency
When warehouses store excessive idle inventory, operational efficiency declines. Space that could be used for high-demand stock gets taken up by unsold or obsolete items. This leads to longer retrieval times, higher labor costs, and an increased risk of mismanagement. Inefficient warehouse layouts and cluttered storage areas create bottlenecks that impact overall productivity.
Strategies to Manage Idle Inventory
Effective management of idle inventory helps manufacturers free up capital, lower overhead costs, improve warehouse efficiency and contribute towards industrial circular supply chain. By implementing the right strategies, idle stock can shift from a liability to an opportunity. To achieve this, focus on the following:
1. Enhance Forecasting and Demand Planning
Accurate forecasting is essential to preventing idle inventory. By leveraging real-time data and predictive analytics, manufacturers can better align production with actual market demand. Integrated enterprise resource planning (ERP) systems and AI-driven forecasting tools help businesses adjust procurement strategies, optimize stock levels, and reduce excess inventory accumulation.
2. Streamline Supply Chain Processes
Supply chain efficiency often contributes to idle inventory buildup. Adopting lean manufacturing principles, just-in-time (JIT) inventory strategies, technology, and improved supplier collaboration help optimize stock movement and prevent overproduction. By reducing lead times and ensuring faster inventory turnover, manufacturers can minimize bottlenecks that cause raw materials, work-in-progress (WIP), or finished goods to remain idle.
3. Liquidation and Asset Recovery Options (Last Resort)
When idle inventory cannot be reintroduced into production or repurposed, liquidation and asset recovery provide cost-effective alternatives. Selling surplus stock through secondary markets, auctions, or specialized industrial liquidation platforms allows businesses to recover a portion of their investment while freeing up warehouse space.
Enterprise manufacturers partnering with industrial liquidation firms gain access to accredited industrial buyers. By evaluating market trends and demand for surplus industrial equipment, businesses can unlock the capital value of idle inventory and reinvest capital into higher-priority initiatives.
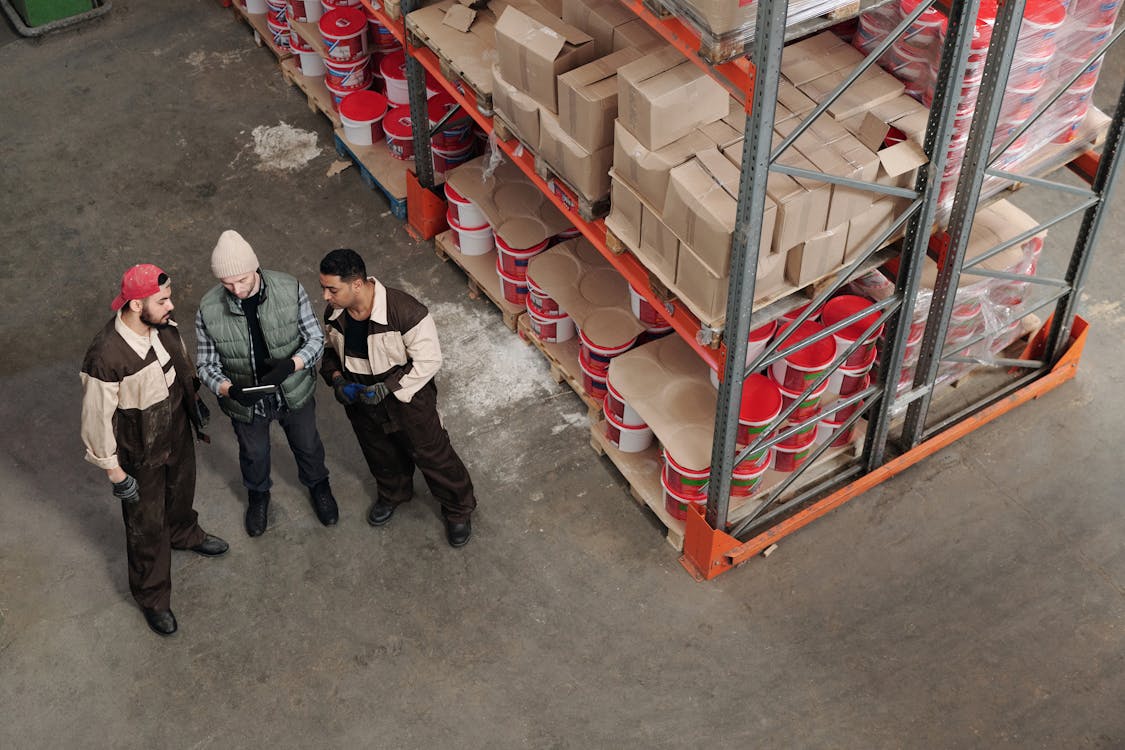
Unlock the Value of Idle Inventory- How Amplio Can Help
Idle inventory is more than just unused stock, it impacts cash flow, warehouse efficiency, and overall profitability. Identifying the causes, knowing the impacts, implementing proactive management strategies, and leveraging asset recovery solutions can reduce and transform idle inventory into a valuable resource.
With a data-driven approach, Amplio streamlines the entire asset recovery process, helping both sellers and buyers maximize value.
For Idle Inventory Sellers
Amplio’s turnkey asset recovery process for industrial sellers ensures that idle inventory is efficiently appraised, marketed, and sold to accredited US buyers, helping businesses recover value.
For Industrial Buyers
Finding high-quality surplus equipment and components at competitive prices can be challenging. Amplio connects dedicated buyers with vetted, high-value inventory, providing cost-effective procurement solutions that support operational efficiency.